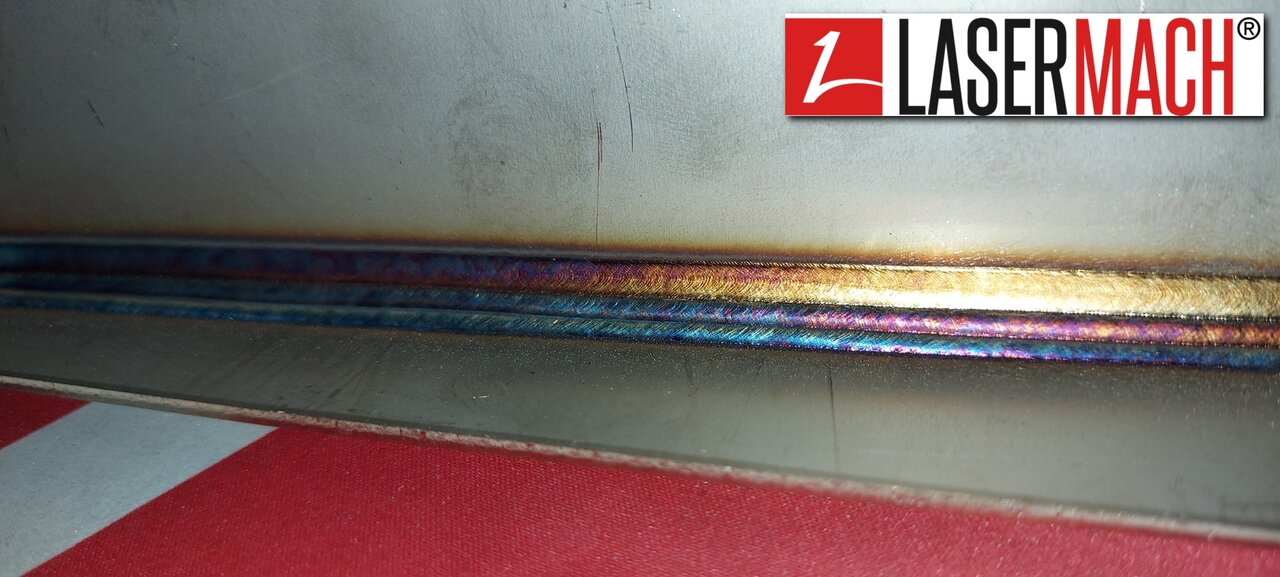
Procesvoordelen van laserlassen met dubbele draad
Hoge lassnelheid en hoge neersmeltsnelheid zijn de grootste voordelen van laserlassen met dubbele draad.
Procesvoordelen van dubbele draadaanvoer
breed werkbereik dat over het algemeen kan worden onderverdeeld in twee categorieën: het lassen van plaatwerk met hoge snelheid en het lassen van dikke platen. Op plaatwerk wordt het proces vaak uitgevoerd met lassnelheden van meer dan 250 cm/min op dun plaatmateriaal. Op dik plaatmateriaal overtreffen de neersmeltsnelheden de standaard laserlasresultaten aanzienlijk.
Toepassingen met hoge lassnelheid
De mogelijkheid om de totale lasenergie over twee afzonderlijke lasdraden te verdelen, biedt unieke voordelen voor lassen met hoge snelheid. Wanneer lasbewerkingen worden uitgevoerd om de lassnelheid te verhogen op dunne metalen componenten in industrieën zoals de automobiel-, tank- en algemene plaatbewerking, worden lasbewerkingen geconfronteerd met een of twee kwaliteitsproblemen: doorbranden of een gebrek aan lasmetaalvolgeigenschappen.
Het laserlasproces met dubbele draad pakt beide snelheidsbeperkende problemen aan. De mogelijkheid om de benodigde lasenergie over twee lasdraden te verdelen, maakt het mogelijk om de benodigde penetratie te genereren terwijl aan de achterkant van de laspoel extra vulling ontstaat. Dit dubbele draadgedrag in de gedeelde laspoel zorgt voor uitstekende spleetvullende eigenschappen. Verbeterde spleetvullende eigenschappen zijn met name waardevol voor industrieën die grote volumes gestanste of gevormde onderdelen verwerken.
Toepassingen met hoge neersmeltsnelheid
Het dubbele draadaanvoerproces kan gemiddeld een toename van 30-80% in het neersmeltpotentieel opleveren in vergelijking met conventionele enkeldraadsprocessen. Het dubbele draadaanvoerproces maakt doorgaans gebruik van draad met een gemiddelde diameter. Naarmate er meer lasenergie wordt toegepast op de elektroden met een kleine diameter (1,2 - 1,6 mm), stijgt de afsmeltsnelheid van de draad exponentieel. De resulterende afsmeltsnelheid van de draad bij een gegeven energieopname is iets lager bij dubbeldraadslassen dan bij een enkele elektrode met een grote diameter. Dit hogere afsmeltpotentieel en lagere energieopname bieden unieke voordelen voor de zware plaatverwerkende industrie. De hoge neersmeltsnelheid biedt uiteraard de mogelijkheid tot een verbeterde productiecapaciteit. De lagere warmte-inbreng kan effectief worden benut om plaatvervorming en de tijd tussen de lasgangen te verminderen bij het regelen van de temperatuur tussen de lasgangen bij meervoudige lasgangen. Het proces kan lassen van röntgenkwaliteit produceren met uitstekende mechanische eigenschappen.
De voordelen van dubbel laserlassen in één oogopslag
- Grote naadvulcapaciteit
- Meerdere lagen mogelijk
- Grote lasnaadvulcapaciteit (2 x 1,6 mm draad = 2,5~3,0 mm naadvulcapaciteit)
- Extreem hoge lassnelheden
- Extreem hoge neersmeltsnelheid
- Kan worden gebruikt op dunne en dikke platen
- Grote kans op kostenbesparing
- Eenvoudig te bedienen
- Twee afzonderlijke draadaanvoerunits, maar elke draad kan onafhankelijk worden aangestuurd
- Wanneer er niet in de dubbele lasmodus wordt gelast, kunnen beide draadaanvoerunits worden gebruikt om te worden voorbereid op een ander materiaal (bijv. roestvrij staal op 1 en aluminium op 2), zodat de omschakeling van het ene naar het andere materiaal ZEER kort is.
Multiwire laser welding for increased gap bridgability
PhotonWeld Laser welding: Filling the gaps
Double wire laser welding, also known as laser beam welding with two wires, is a laser welding process in which two wires are melted simultaneously using a laser beam to join two metal parts. This method is commonly used in welding applications that require high productivity, speed, and quality or especially when a big gap between the components must be filled. with double wire feeding the Photonweld laser welding machine can fill easily a gap of 2 mm.
The process of double wire laser welding is characterized by a high power density laser beam that is focused on the welding area, creating a small and intense heat source. This high heat input enables the simultaneous melting of two wires, which then join together to form a strong bond.
The advantages of double wire laser welding include increased welding speed, improved welding quality, and reduced material waste. The high speed of the laser beam allows for fast and efficient welding, which can significantly increase productivity. Additionally, the precise control of the laser beam allows for precise and accurate welding, which leads to improved welding quality and reduced defects.
However, there are also some challenges associated with double wire laser welding. One challenge is the selection of appropriate welding parameters, such as laser power, welding speed, and wire feed rate. Another challenge is the need for a higher level of technical expertise to operate the laser welding equipment and control the welding process.
Twin Wire Feed Means a Greater Ability to Fill the Wire and to Weld Wider Seams. According to Our Test Data, if You Use a Single-feed Laser Welding Machine Can Only Weld a Maximum of 1.5-1.8mm Seams. However, with a Double-feed Laser Welding Machine, a 3-4mm Wide Seam Can Be Welded.
Twin Wire Feed Also Means That Thicker Materials Can Be Welded. This is Because More Wire Filling in the Welding Process Makes the Welding Joint More Stronger,Stable, and Reliable.
In conclusion, double wire laser welding is a highly efficient and effective welding process that has many advantages over traditional welding methods. However, it requires specialized equipment and expertise to achieve optimal results.