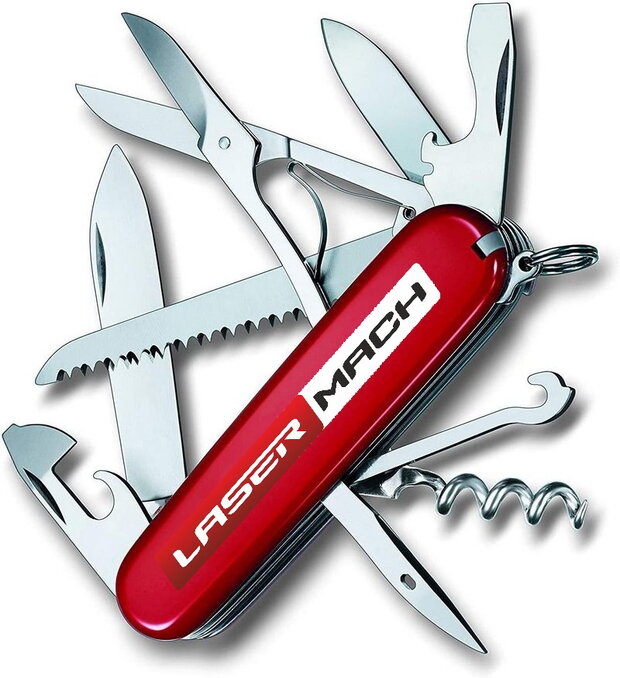
Portable Multifunction Laser Welding Machines
PhotonWeld Series:
The Swiss army knifes for the metal Worker!
TEN in ONE Multitool
1 - Laser Welding without material infeed
2 - Laser Welding with material infeed
3 - Laser Welding of dissimilar metals
4 - Laser Spot Welding
5 - Laser Fish Scale Welding
6 - Laser Stitch Welding
7 - Laser Cutting
8 - Laser Cleaning
9 - Laser Deburring
10 - Laser Edge Rounding

A WORLD-CLASS LASER WELDING MACHINE MANUFACTURER
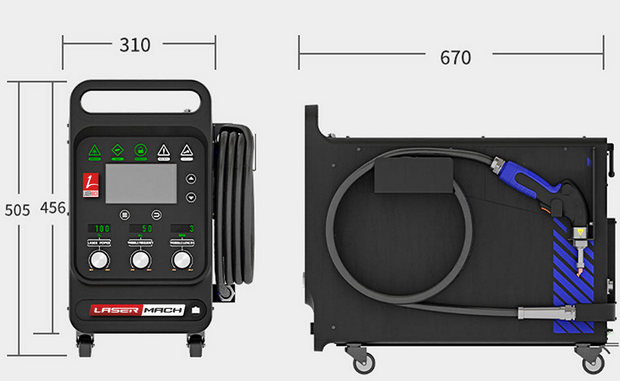
Compact and Portable Laser Welding Machine
PhotonWeld A-PRO : "Smart" Made more simple
EXPLORE YOUR OPTIONS
Select the Perfect System for Your Needs
Serie PhotonWeld A-PRO | PhotonWeld A-PRO-T45 | PhotonWeld A-PRO-T55 | PhotonWeld A-PRO-T70 | PhotonWeld A-PRO-T90 | |
---|---|---|---|---|---|
Max Welding Penetration - Single side Welding | |||||
Stainless Steel | 4,5mm | 5,5mm | 7,0mm | 9,0mm | |
Carbon Steel | 4,0mm | 5,5mm | 7,0mm | 9,0mm | |
Cortensteel | 3,0 mm | 4,0 mm | 5,0 mm | 6,0 mm | |
Galvanized steel | 3,5mm | 5,0mm | 6,0mm | 7,0mm | |
Aluminium 3000/5000 | 3,5mm | 5.0 mm | 6,0mm | 7,0mm | |
Aluminium 6000 series | 2,5 mm | 4,0 mm | 5,0 mm | 6,0 mm | |
Brass | 2,0 mm | 2,5 mm | 3,5 mm | 4,5 mm | |
Copper | 1,5 mm | 2,0 mm | 3,0 mm | 4,0 mm | |
Titanium | 3,0 mm | 3,5 mm | 4,5 mm | 5,0 mm | |
Zink >98% | 2,5 mm | 3,0 mm | 3,5 mm | 4,0 mm | |
Fibre cable length | 5/10/15 m | 5/10/15 m | 5/10/15 m | 5/10/15 m | |
Power supply cable | 10m | 10m | 10m | 10m | |
Weight | 43kg | 44kg | 46kg | 48kg | |
Dimensions (L-H-W) | 673-480-310mm | 673-505-310mm | 673-505-310mm | 673-505-310mm | |
Operating temperature | -20 ~ +60°C | -20 ~ +60°C | -20 ~ +60°C | -20 ~ +60°C | |
Noise level | < 58 dB | < 58 dB | < 58 dB | < 50 dB | |
Power connection | 220V - Mono - 12A | 220V - Mono - 16A | 220V - Mono - 19A | 220V - Mono - 20,8A | |
Applicable wire diameter | 0,8/1,0/1,2/1,6 mm | 0,8/1,0/1,2/1,6 mm | 0,8/1,0/1,2/1,6 mm | 0,8/1,0/1,2/1,6 mm | |
Predefined Welding Parameters | 24 | 30 | 40 | 40 | |
Free programmable welding Parameters | 20 | 20 | 20 | 20 | |
Active cooling with Inverter driven compressor and servo driven ventilators | |||||
Maximum Welding Thickness is depending of the material quality |
1 - PhotonWeld: Laser Welding without material infeed
⇒ Laser Welding without added material : Autogenous Laser Welding
Materials are joined without the addition of extra materials which requires the highest level of fixturing and joint preparation. Since no material is added, it is necessary for the materials to be welded to remain in intimate contact during the welding process. Any significant separation of the materials can result in an unacceptable weld profile.
Good Fixturing to ensure consistent fit-up of the weld joint is a key to successful fiber laser welding. An important benefit of fiber laser is that the welded joints have an exceptional cosmetic appearance. In some cases, these welds are almost perfectly blended with the surrounding material. Depending on the fixturing and joint fit-up, some welds may have small amounts of concavity (which may not be acceptable for product designs that require fatigue properties similar to those of the base material) or convexity.
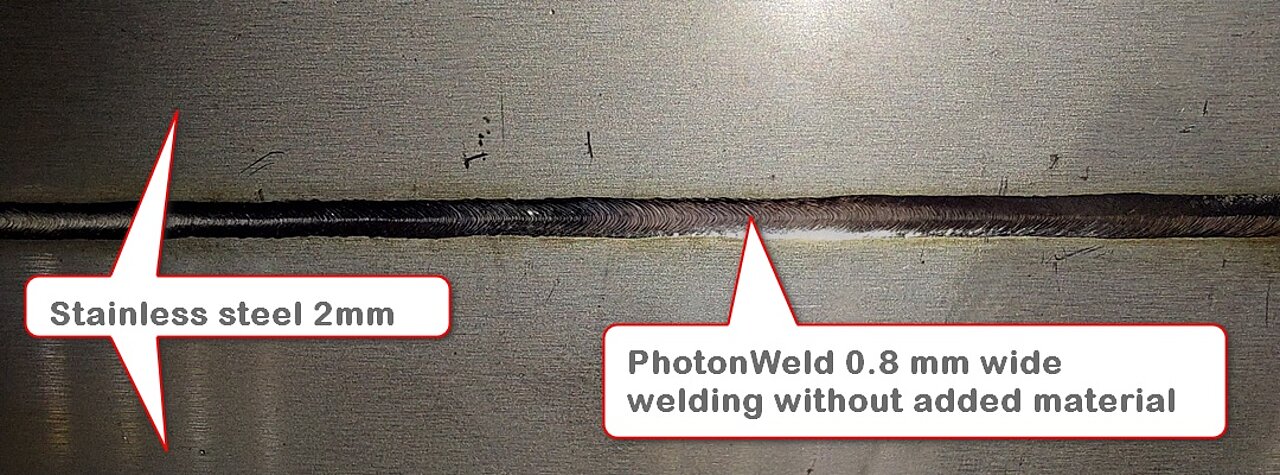
2 - PhotonWeld: Laser Welding with material infeed
⇒ Welding WITH added material : Additive Laser Welding
Material is added to the weld joint usually in the form of metallic wire.
Three reasons for adding material to the weld are:
- Joint fit-up: By adding extra material, the joint becomes more tolerant to joint mismatch. Acceptable welds may be produced from joints with less than perfect fit-up.
- Weld geometry: Addition of filler metal is used to control the shape and size of the weld. Maintaining a crown (convex surface of the weld) creates a reinforcement which is important for joints requiring mechanical strength and fatigue life in the overall product’s design performance.
- Dissimilar metals: Filler metal is added to facilitate welding of dissimilar metals and alloys which are otherwise metallurgically incompatible.
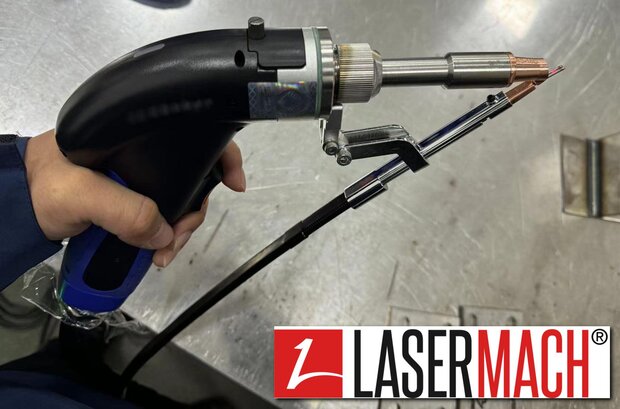
Multiwire infeed laser welding for increased gap bridge-ability
PhotonWeld Laser welding: Filling the welding gaps with double wire
Click here for more info
3 - PhotonWeld: Laser Welding of dissimilar metals
Laser Welding of dissimilar metals works perfect with our wobble laser welding machine
Dissimilar Metal Welding - Different metals perfect joining by Fiber laser
As with any welding process, establishing a good fiber laser weld involves a lot of variables. A material’s weldability is a factor. Most common materials a fab shop will process—be it carbon steel, stainless, or aluminum—have been successfully laser welded for years, using both continuous wave and pulsed modes. Lasers have performed dissimilar-metal welding ( Sample picture is copper joined with galvanised steel by fiber laser welderwithout adding material), and specialized weld joint designs in galvanized material have even accounted for zinc outgassing. Moreover, a multikilowatt fiber laser has been shown to successfully weld even the most challenging of materials, including copper
4 - PhotonWeld: Laser Spot Welding
⇒ Laser Spot Welding - Laser Keyhole Point Welding
Laser Keyhole welding beats conventional spot welding machines on all fronts
Laser spot welding is a non-contact process which uses a laser to create a single weld spot to weld metals together. Lasers are capable of delivering a pulse of light with accurate, repeatable energy and duration. When the pulse is focused into one place – a small spot – (adjustable anywhere from approximately 0.1 to 5.0 mm) on the part, the energy density becomes quite large. The light is absorbed by the material causing a “keyhole effect” as the focused beam drills into, vaporizes, and melts some of the metal. As the pulse ends, the liquefied metal around the keyhole flows back in, solidifying and creating a small spot weld. This entire process just a few milliseconds.Laser keyhole spot welding offers numerous benefits in the right applications, including precise control of penetration depth, a very small beam size for a small heat-affected zone, great consistency, and an extremely fast process.
Most manufacturers are looking for ways to save money and improve efficiency without negatively impacting quality. Manufacturing operations that are using resistance spot welding can reap significant productivity and quality benefits in some applications by converting to laser keyhole spot welding. Lasers can fire many pulses per second, and, by moving either the work piece or optics, allow either separate “spot” welds or a series of overlapping spot welds to create a laser seam weld that can be structurally sound and/or hermetic.
Implementing fiber laser keyhole spot welding can result in a welding process that is three to four times faster compared to resistance spot welding, while also increasing weld quality and repeatability.
However, laser keyhole spot welding may not be the right fit for every job.
5 - PhotonWeld: Fish Scale Welding
⇒ PhotonWeld: Fish Scale Welding
Laser Fish Scale welding beats conventional TIG welding machines on all fronts
Fish scale welding is considered to be one of the most effective methods for improving the integrity and quality of the weld bead. However, it requires a high level of expertise and a long and painstaking welding process. Consequently, fiber lasers, with the advantages of high precision, high efficiency, and good repeatability, are commonly preferred to manual techniques.
6 - PhotonWeld: Stitch Welding - Intermittent Weld
⇒ Laser Stitch Welding -
Many engineers and welders find themselves confused with the difference between stitch welding and seam welding since they are often used interchangeably, but there is a definite difference between the two types of welds. In the welding world, it is important to distinguish the two because both welds are have different strength properties and are used for different purposes.
Stitch Weld, Also known as intermittent weld or called skip Welding. Stitch welding is not a continuous weld across a joint, but a weld broken up by space gaps in between welds, which results in a “stitch” look. It is not as robust and durable as a seam weld. It is used to prevent heat distortion and to also reduce the cost of welding if a long continuous weld is not necessary.
There are two common types of stitch welds, fillet weld and butt joint weld.
-
A fillet weld is a triangular seam weld that joins two surfaces at right angles to each other.
-
Butt welds are generally in a lap joint, T-joint, or corner joint, which is most common amongst welding pipe or tubes to another surface where two pieces of metal are positioned coplanar and touching on one edge.
7 - PhotonWeld: Laser Cutting
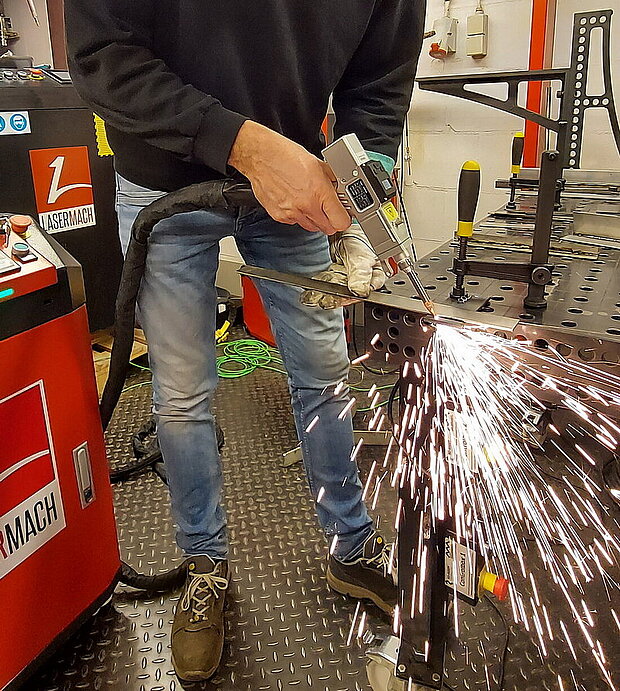
PhotonWeld : Laser-Cutting by hand
Now Our PhotonWeld version can cut easily steel plates from the free hand.
Straight lines, contours, almost every metal and every form can be cut with our handheld Laser welding Machine!
No more limits in your creativity and productivity!
Hand-operated laser cutting
First real laser welding-cutting combi machine that works safely and good!
8 - PhotonWeld: Laser Cleaning
⇒ What can a laser cleaner clean?
Laser ablation coating removal
Laser coating removal is an ablative process whereby laser energy is focused and absorbed by the surface, resulting in vaporization of the coating with minimal effect to the underlying substrate. This process can be applied to various materials including metal, plastics, composites and glass.
Laser cleaning is a green and environment friendly cleaning method, because laser removal can replace the use of chemical and abrasive cleaning method, this cleaning method will harm the material base and lead to some pollution, meanwhile the laser cleaning machine is a non-contact cleaning process. So there is no secondary waste after the cleaning work.
Laser cleaning is a green cleaning method, it can be used to remove dust and rust in the metal and none metal material. For example, the laser cleaning machine can work on plastic injection molds, rubber molds. And the laser cleaning machine is also a good cleaning tool for metal substrate and product pieces, the laser cleaning system can remove rust and dust and oxide deposition quickly and entirely, and the laser cleaner also clean the resin surface, oil stains, dirt, rust, coating, paint on all kinds of metal, cleaning a rusty grille down to a shiny metal.
9 - PhotonWeld: Laser Deburring
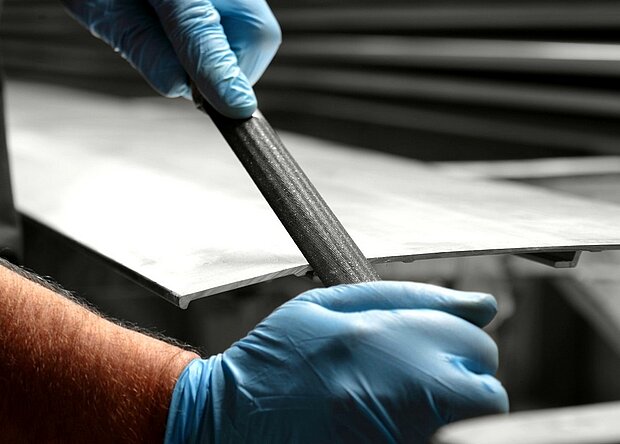
⇒ Parts deburring by laser
⇒ Laser Deburring: Thermal deburring process where a laser beam of lower intensity than in conventional laser cutting and is directed towards the workpiece burrs.
The process: It has been found that laser deburring provides reasonably accurate dimension and minimal size of HAZ, thus minimal material property changes. . Furthermore, for special applications such as burrs around intersecting holes, a situation in which no mechanical deburring tools are effective, laser deburring would have an advantage over conventional deburring techniques.
The method uses a laser for welding with settings similar to the processes used for laser welding. The difference is mainly that the laser beam intensity in this method is slightly lower to reduce the risk of new burrs forming due to heat generation. The focus point is also a bit above the surface to give a wider beam at the point of impact. The laser beam is directed towards the burrs of the workpiece so that they are burned due the intensity of the laser.
10 - PhotonWeld: Edge Rounding
⇒ Edge Rounding: allowing for optimal coating coverage and corrosion protection.
Edge rounding (also known as edge radiusing) is the process of removing the vertical burrs, nibble marks, or scallops on the holes and edges of a deburred metal part. Metalworkers use edge rounding to break the edge of processed components, allowing for optimal coating coverage and corrosion protection.
Metal edge rounding is a versatile process that can be used to support a variety of metalworking projects. Generally, this solution is ideal for creating the best possible finish on laser-cut or machined metal parts. Edge rounding is a fast and efficient way to remove imperfections from parts with sharp edges or holes across many industries, ranging from automotive to healthcare.
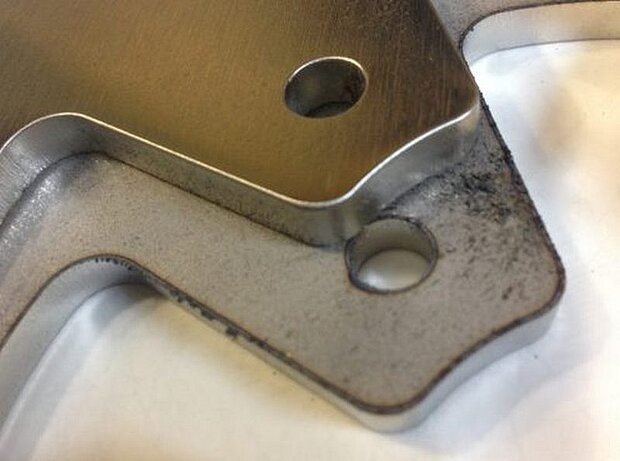
Part Strength & Durability
Rounded metal parts will bond correctly with coatings, increasing their surface strength and durability in the process. (This is especially important for high-contact components.) Fully coated parts are more resistant to corrosion, operational wear and tear, abrasion, and many other types of damage
Part Aesthetics
Rounding metal parts allows them to be properly coated and painted, creating functional products with an attractive aesthetic. Metal components free of sharp edges create a perfect bonding surface for paints, reducing the risk of peeling and being forced to reapply paint coatings over time.
Physical & Electrical Properties
Rounded metal parts are compatible with a wide range of protective coatings, including those that support electrical conductivity, heat resistance, and cryogenic stability. For these protective coatings to bond properly, each metal part must be completely free of burrs, scallops, and other surface imperfections.
Applications of Metal Edge Rounding
Metal edge rounding is a versatile process that can be used to support a variety of metalworking projects. Generally, this solution is ideal for creating the best possible finish on laser-cut or machined metal parts. Edge rounding is a fast and efficient way to remove imperfections from parts with sharp edges or holes across many industries, ranging from automotive to healthcare.
One unique application of metal edge rounding is creating an ideal finish on parts with unique cosmetic requirements. For example, a modern edge rounding tool can round the edges of a stainless steel part without marring its surface or tearing off any protective sheeting.
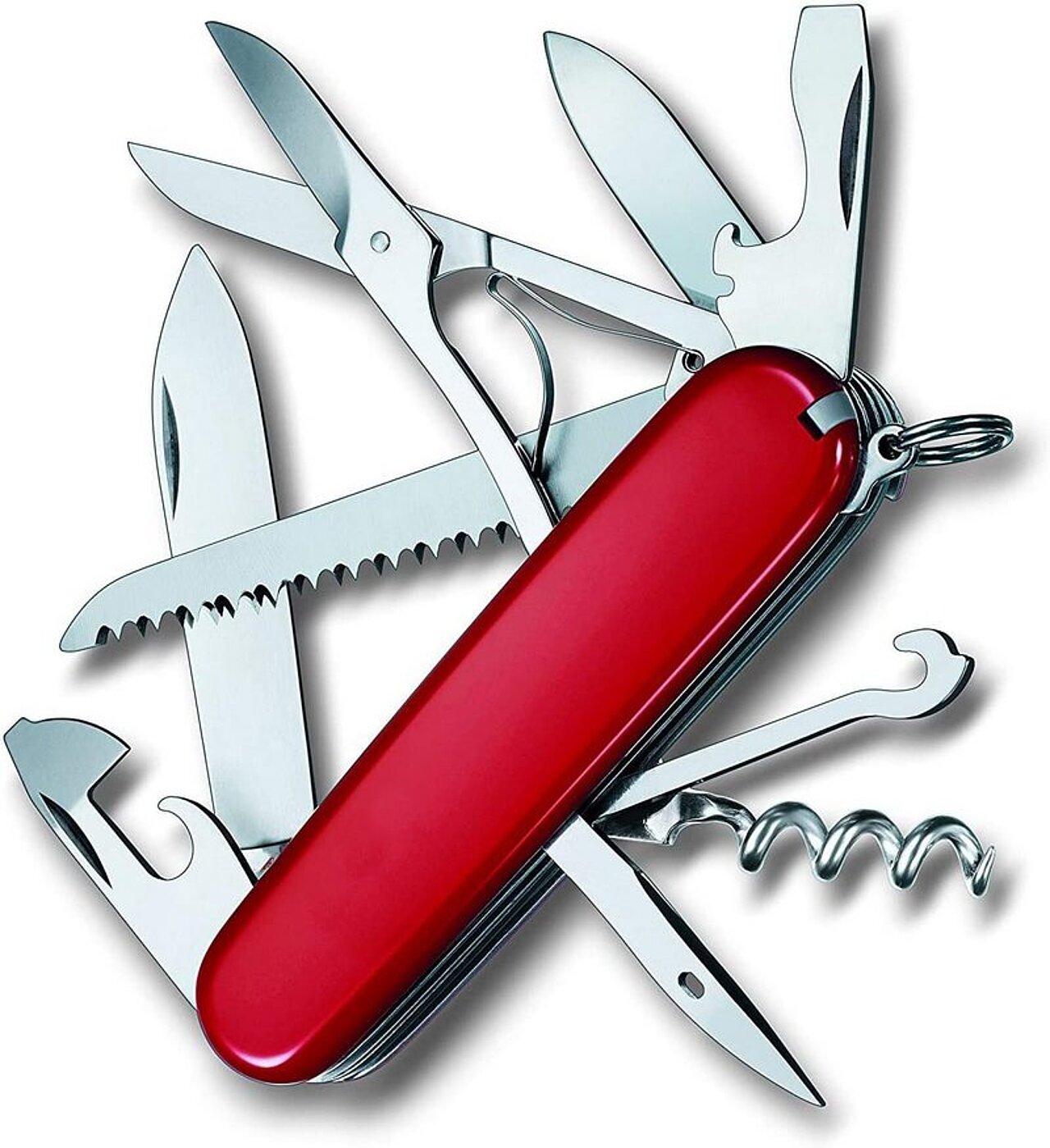
PhotonWeld A-Series = 10 in 1 = Multifunctional Tool
Welding with wire infeed - Welding without Wire infeed - Spotwelding - Stitch Welding - Fish Scale Welding - Dissimilar material Welding - Cutting - Cleaning - Deburring - Edge Rounding
PhotonWeld Series = 10 in 1 = Multifunctional Tool
PhotonWeld A-Series:the Swiss army knife for the metal Worker!
1 - Laser Welding without material infeed
2 - Laser Welding with material infeed
3 - Laser Welding of dissimilar metals
4 - Laser Spot Welding
5 - Laser Fish Scale Welding
6 - Laser Stitch Welding
7 - Laser Cutting
8 - Laser Cleaning
9 - Laser Deburring
10 - Edge Rounding
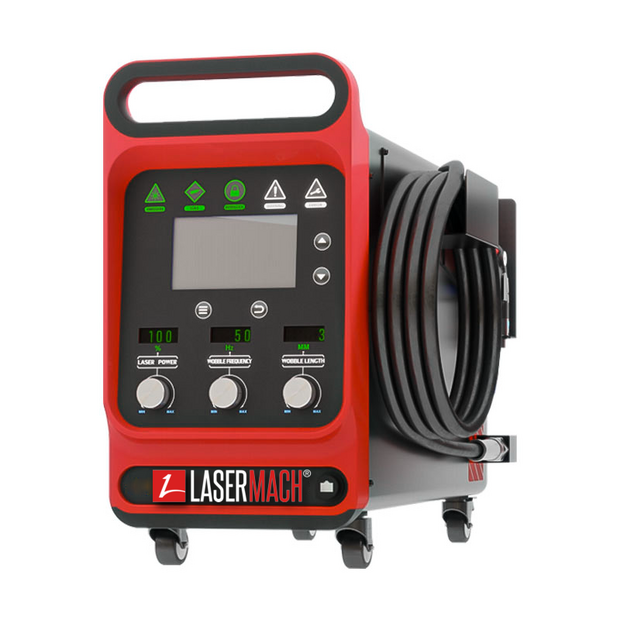
PhotonWeld © portable fiber laser handheld welder based on 976nm pump technology
The current laser welder equipment in the market are mainly water-cooled solutions, that is, heat is taken out of the laser through the external circulation of the chiller. Lasermach's PhotonWeld focuses on continuous discussion and innovation based on 976nm technology, combined with the high photoelectric conversion efficiency of 976nm Creatively solved the problem of air-cooled refrigeration capacity, launched the air-cooled 976nm technology for the first time in the industry, solved the power consumption and portability issues, and once again lead the technical development direction of fiber lasers.
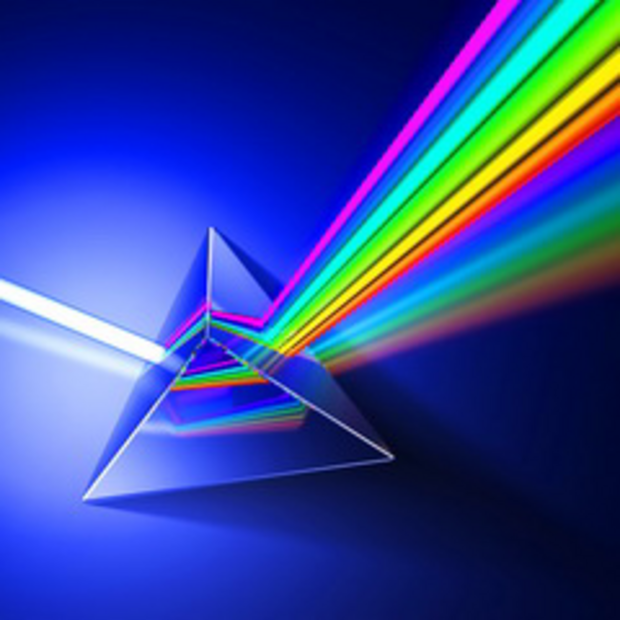
The FIRST Truly Portable Continous Wave Wobble Laser Welder
PhotonWELD is FASTER and Easier than Traditional MIG & TIG Welding and is much faster than a non continous wave laser welder
PhotonWELDTM handheld laser welding is easy to learn, simple and fast to set up and provides consistent high-quality results across a wide range of materials and thicknesses
Experienced MIG and TIG users benefit from the more rapid and flexible processing capabilities of PhotonWELD:
- Up to 7X faster than TIG
- Up to 4X faster than Quasi CW Laser welders with only pulse welding for power over the 350 Watt
- Easy to learn and operate with highest process consistency
- High quality welding of thick, thin and reflective metals without distortion, deformation, undercut or burn-through
- Welding of dissimilar metal parts of different thicknesses
- Dramatically low heat input and minimized heat affected zone
- Minimal part setup and post-processing grinding or polishing
- Increased productivity with no need for machining or straightening deformed parts
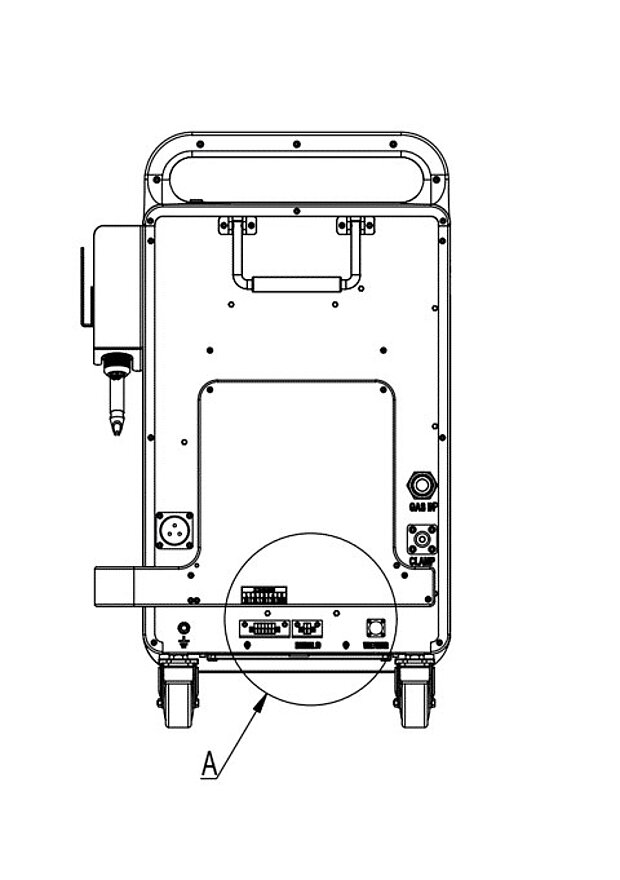
PhotonWeld A-Pro T-Series
Available with Optional COBOT ROBOT interface
Start your automation with your own existing Robot.
Connect our Photonweld A-Pro T-Series to any Robot and Cobot.
Very simple and easy interface.
No need for high level programming!
Need only 5 contacts from your robot or cobot.
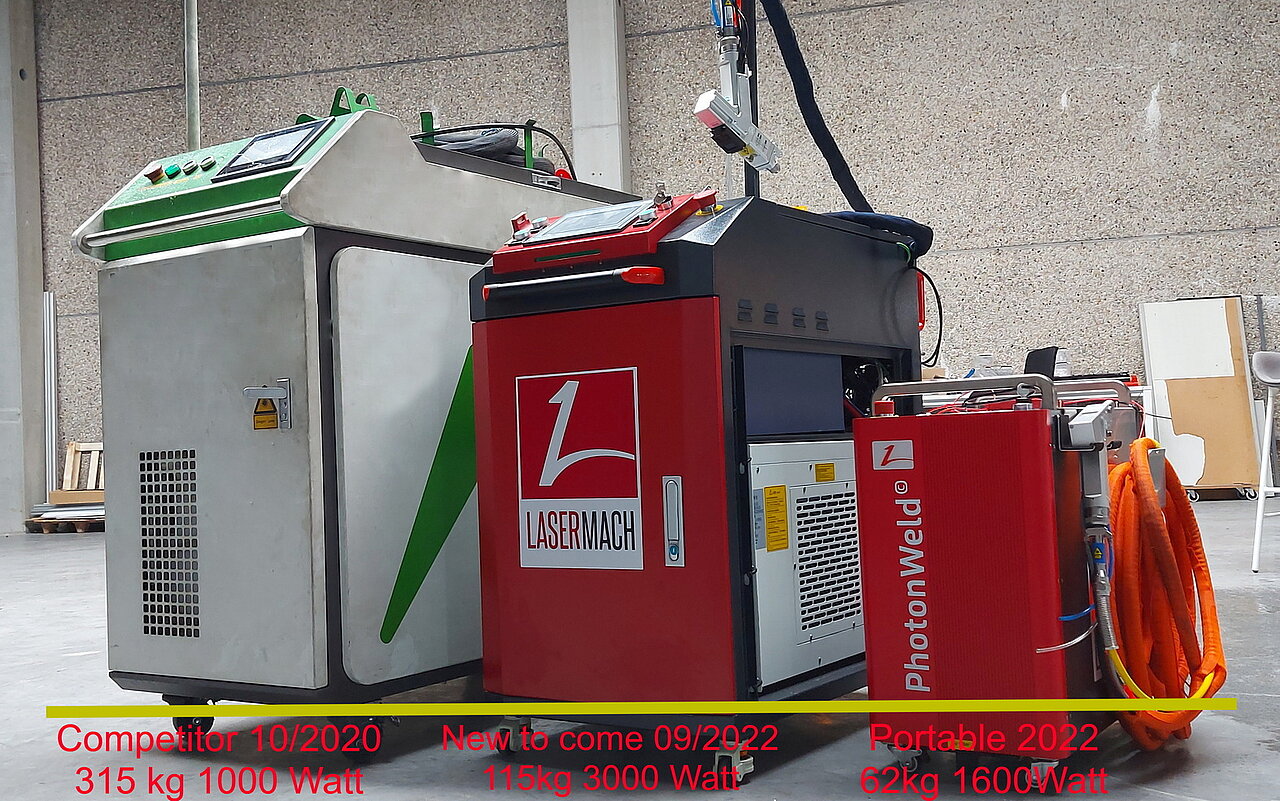
PhotonWeld Series: The Very best REAL Portable Handheld Laser Welding Machine
PhotonWELD TM handheld laser welding is easy to learn, simple and fast to set up and provides consistent high-quality results across a wide range of materials and thicknesses
PhotonWeld: SIMPLY "THE" BEST
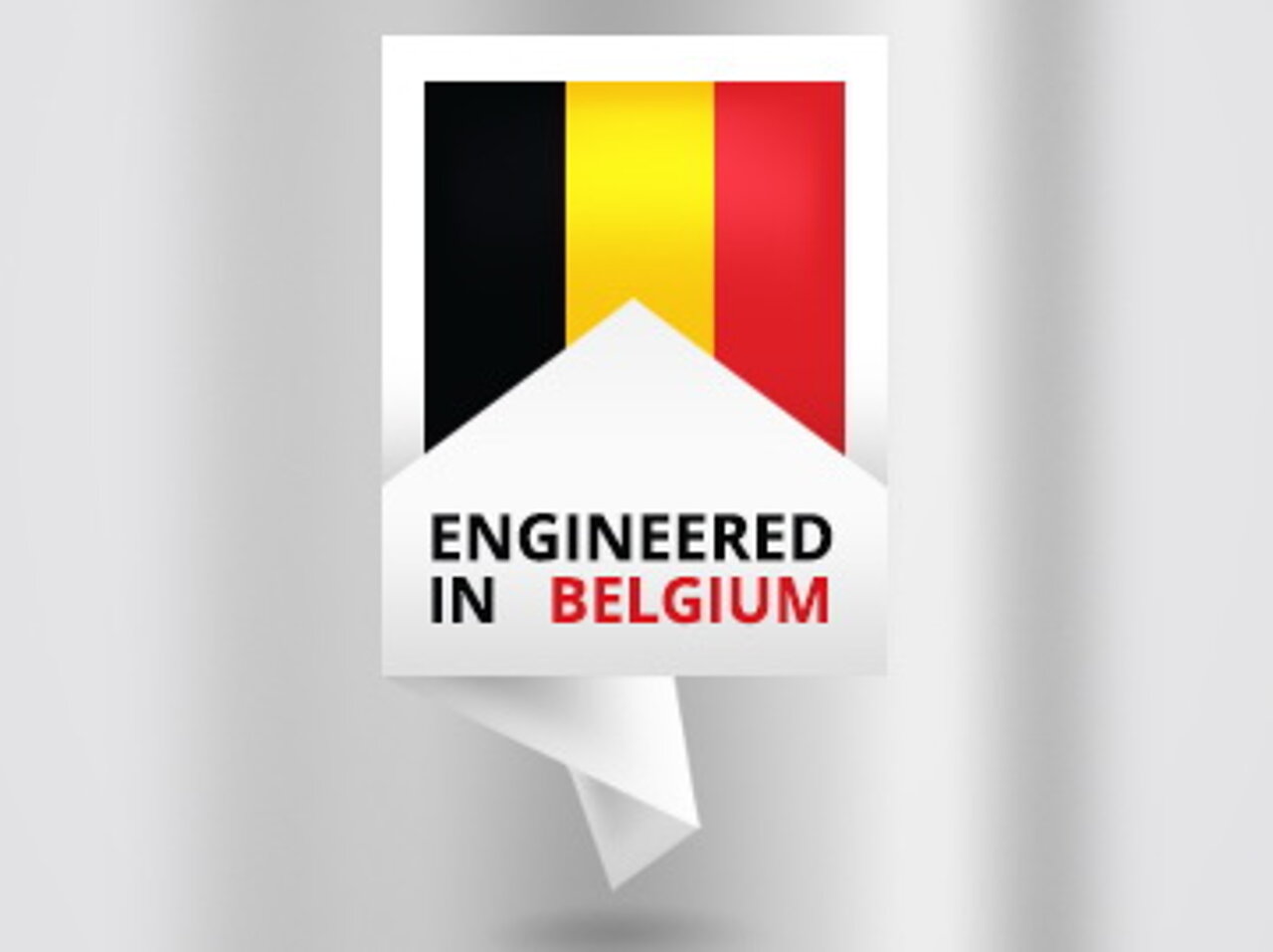
ENGINEERED and DESIGNED in BELGIUM
High Tech Designed in Europe
