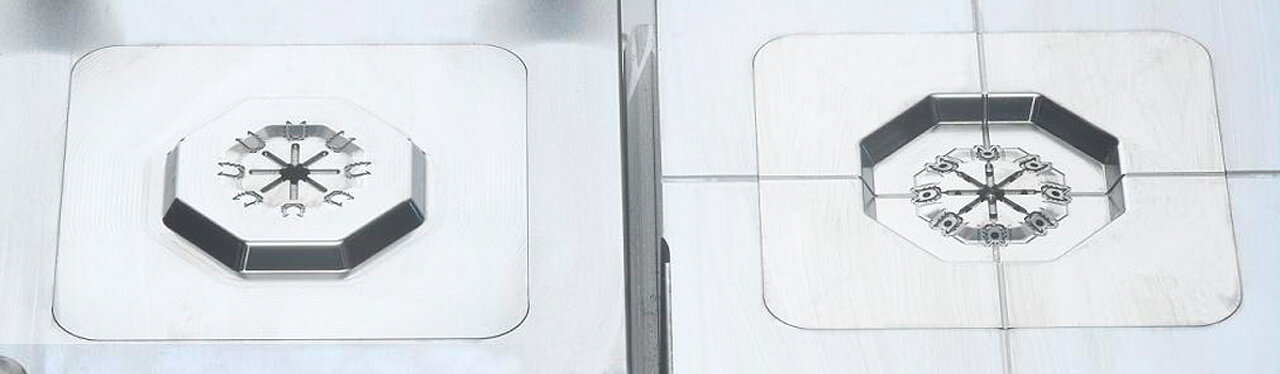
Why Laser Welding for the Tool & Die Industry?
The tool and die industry is vital for producing components used across automotive, aerospace, and manufacturing sectors. These tools often face wear and damage due to high-pressure operations, leading to production disruptions and costly replacements. Laser welding provides a transformative solution by offering precision repairs, reducing material waste, and extending the lifecycle of tools and dies.
Unlike traditional methods, laser welding is non-invasive and precise, allowing for targeted material deposition. This ensures minimal heat distortion, preserving the tool’s original design and functionality. The ability to perform repairs in-situ also minimises downtime, making laser welding a practical and cost-efficient choice for industries relying on consistent production.
Lasermach Moldmax III series
LW-Moldmax-III Pro and LW-Moldmax-III PRO-Plus Universal Jig Welding Workstation
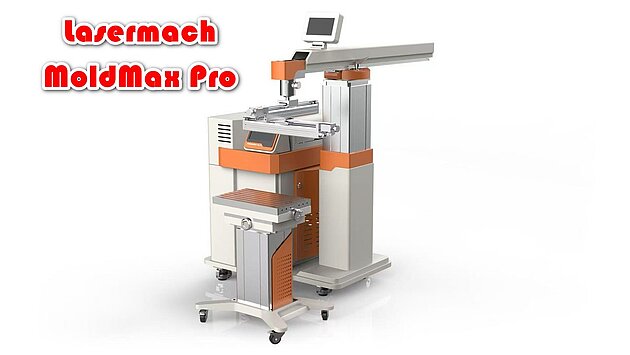
Integrated boom mold welding machine
Z crane arm can rorate 360 degree
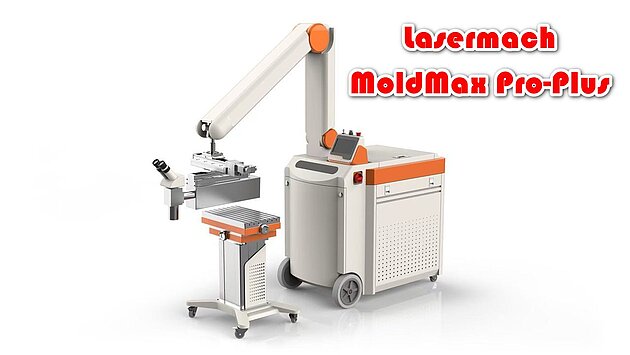
Foldable and retractable boom
Foldable boom mold laser welding machine.
Moldmax-II Pro laser welding machines,
The Best Choice for Mobile Laser Welding using our photonweld technology
From mould repairs to precision reworking in hard-to-reach areas, the MoldMax III-Pro mobile laser welder sets the new standard for flexibility and accuracy in the tool and die industry.
🔧 Weld directly on the machine, no need for disassembly.
🛠️ Easily move between workstations or on-site locations.
👁️🗨️ High precision through motorised X/Y axis and binocular optics.
The Moldmax laser welding machine can be used not only for mould repair and maintenance, but also for repairing parts produced by die casting (again with material input), or for welding mechanical parts in various difficult reachable areas.
Key Applications of Laser Welding in the Tool & Die Industry
Laser welding addresses a range of critical needs in the tool and die sector, including:
Repair of Worn or Damaged Tools
Restore cutting edges, mould cavities, and other intricate areas with unparalleled precision, maintaining original dimensions and functionality.
Custom Tool Modifications
Modify tools for specific applications or upgrades without needing full replacements.
Preventive Maintenance
Conduct targeted repairs to address early signs of wear, extending the lifespan of essential equipment.
Restoration of Moulds and Dies
Reconstruct damaged areas of injection moulds, stamping dies, and extrusion tools, ensuring high-quality production standards.
Welding of Hard-to-Reach Areas
Employ fine laser beams to repair delicate or inaccessible sections of tools and dies.
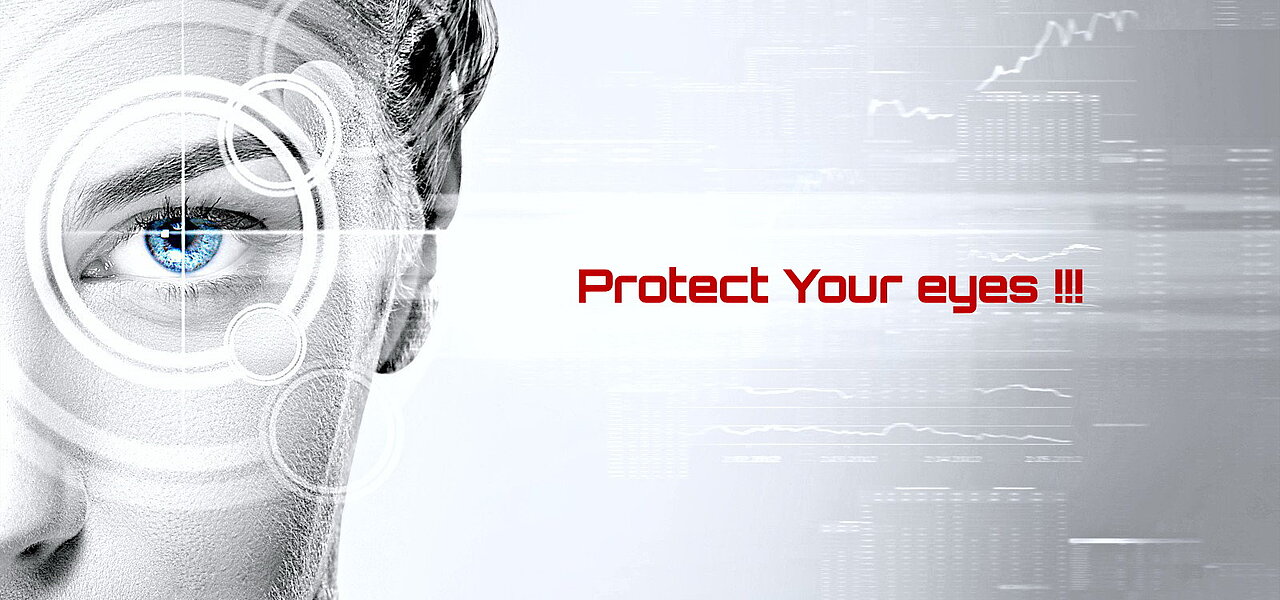
The laser equipment can be very hazardous. Only trained personnel should be allowed to repair the laser equipment. The laser light can cause permanent damage to the eye - the collimated nature of the laser light allows for focusing of the light on the retina in the eye. Direct laser light or scattered laser light allowed to enter the eye can cause partial to total permanent blindness. A laser safety program should be initiated and laser safety training should be given to all individuals before using any laser welding system.
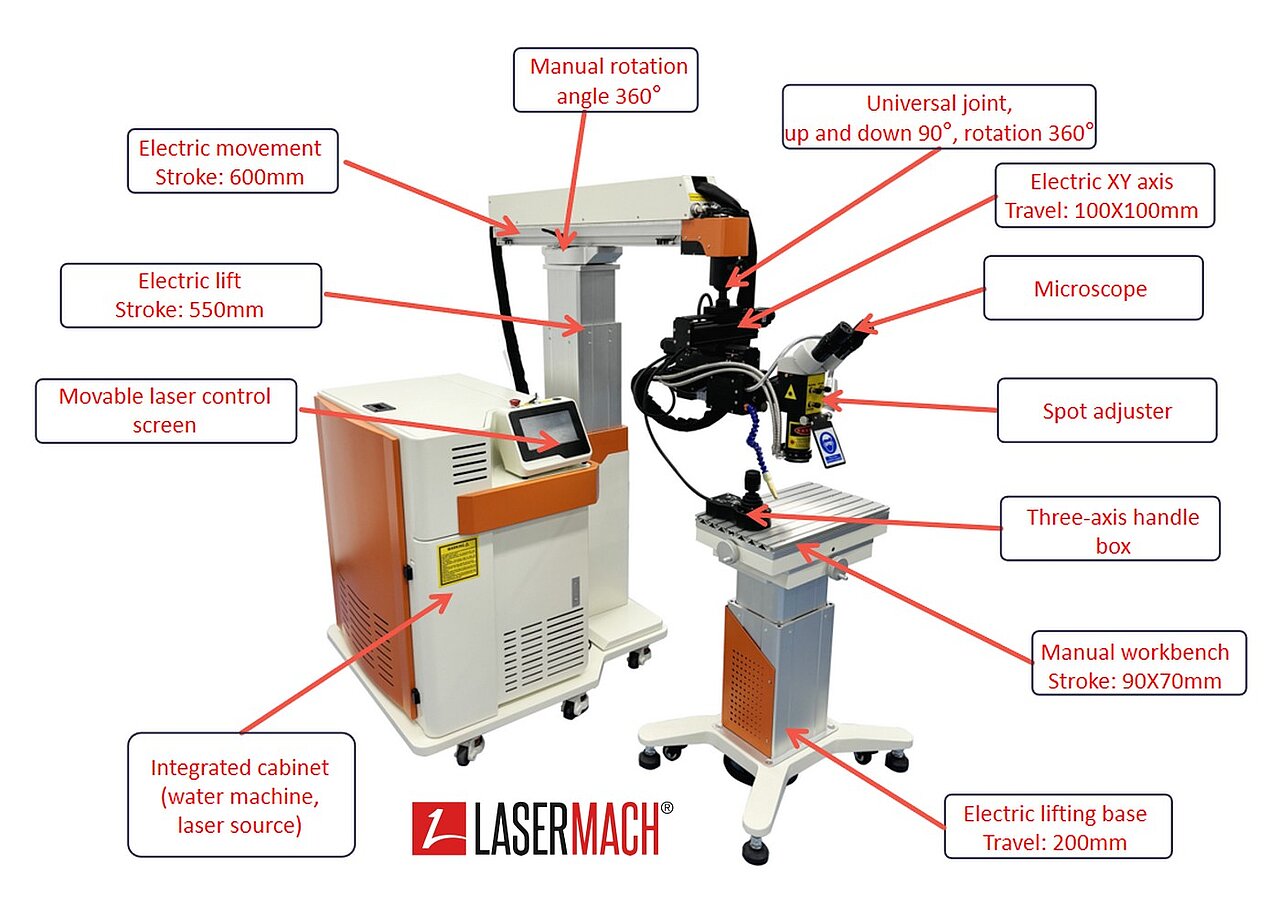
Discover the Lasermach Moldmax laser systems for moulds and moluding
Moldmax laser welding machines using our photonweld technology
Laser systems find many applications in mould making and moulding processes of plastic, rubber, glass or metal materials.
One of the most common uses of laser welding is in the repair and maintenance of moulds by material filling: it is a semi-automatic process in which the operator’s skill is supported by a very stable, repeatable technology and software functionality that facilitates processing.
In addition, the laser has a very localised thermal impact, therefore minimal, leaving the mechanical characteristics of the material unchanged and minimising post-processing activities.
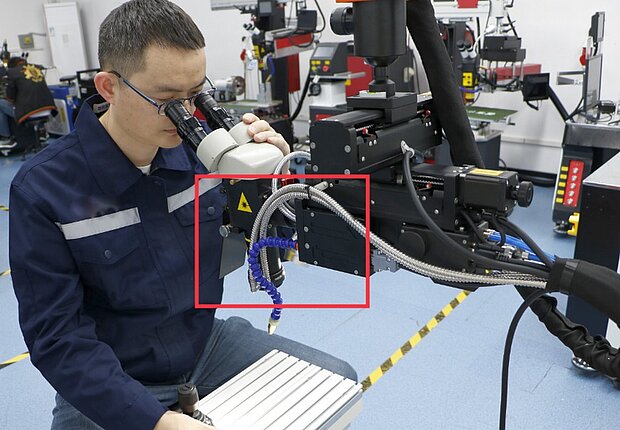
Lasermach offers an extended range of laser welding systems , from simpler and compact models for welding on small molds and inserts, to versions dedicated to machining on medium-sized parts, to the big series that allows maximum flexibility and ease of use even on large molds or huge other parts difficult to move
The Moldmax laser welding machne can be used not only for mould repair and maintenance, but also for repairing parts produced by die casting (again with material input), or for welding mechanical parts in various areas like repairing a cilinderblock from a 12 cylinder motor while not dismounting the motor.
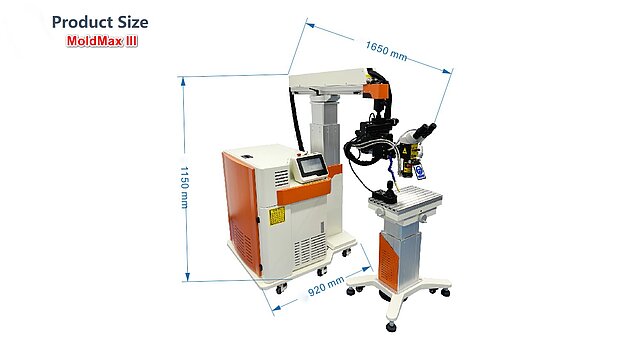
Moldmax laser repairing of molds
Manufacturing moulds and tools can be a costly process, and their service lives are often shortened due to wear and tear, damage, and corrosion. However, laser welding has emerged as a promising solution to significantly enhance the lifespan of moulds and tools through laser deposition welding. The Die Mould Laser Welding Machine, developed by Lasermach, offers exceptional performance and flexibility in this regard.
Our robust and high-performance Die Mould Laser Welding Machine enables the welding of intricate structures that would otherwise be challenging or even impossible to weld using traditional welding technologies. This is particularly advantageous when working with delicate materials such as plastic or glass. With precise control over laser energy and exposure time, the machine allows for welding of metallic materials with high melting temperatures and excellent thermal conductivity. Moreover, it possesses the capability to weld different types of metals, further expanding its versatility.
Lasermach's MoldMax laser welding and mold maintenance system with fiber source.
Moldmax has been specially designed to perform modifications and repairs to molds damaged by wear or use.
The use of lasers, with the addition of materials, has revolutionized the traditional welding techniques of molds, allowing repairs without the need of preheating. This avoids the common collateral damage induced by traditional welding, such as geometric distortions, edge burns and decarburization.
Thanks to the properties of the laser beam, complex areas such as narrow and deep grooves, or internal and external edges, can be welded. The metallurgical quality of the weld meets the highest standards on all steels, copper alloys, and aluminum. The hardness of the welding layers can reach very high values without the need for subsequent heat treatments. Its simple way of operating and perfect visual inspection of the filler material, using a stereomicroscope, make this technology accessible to everyone, without having to rely on highly qualified technicians.
Moldmax is powered by a new generation laser source that offers greater energy efficiency and allows for high productivity.
Productivity
- The new MoldMax introduces more process stability and a high-quality laser beam. These features increase the production rate, while consistently guaranteeing flawless process execution.
Maintenance-free
- The new MoldMax does not have any consumable parts and is maintenance-free. The engineering team has pushed the boundaries of energy efficiency, making this the most efficient MoldMax ever made.
Advanced software functions
- The processing parameters are managed through software that allows any operator to carry out advanced welding operations practically and intuitively. These software functions include welding along circular paths, on inclined planes, filling, and the overlap function for executing extremely regular weld seams.
Tool Steel-
Cold Work : 1.4718, SKD11, Dell, Dc53.
High Speed : 1.3348, SKH 55.
Hot Work : X25CrMoS, SKD61, DHA1, DH2F.
Plastic Work : 1.2311, S45-50-SSC, P-20, NAK80 Px4, Stavax, M300.
Gray Casting Iron – GG 20, GG 25,(FC), GGG 40, GGG 50, GGG 60, GGG 70L, GGG, 90(FCD).
Special Materials – Super alloys, Colmonoy, Stellite, Duplex Stainless steel, Aluminum, Titanium, Inconel alloys, Hastelloy, Ni-Resist, Magnesium, Molybdenum, Nickel, Silver, Tin, Zinc, Silver, Gold.
Special Process – Etching, Mirror finishing.
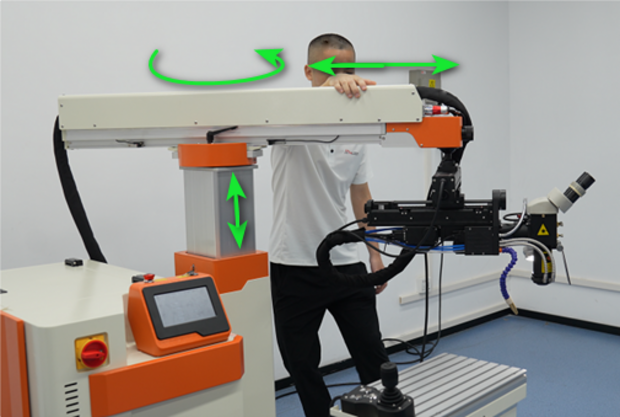
LW-MOLDMAX PRO:
MOBILE MOULD LASER WELDING MACHINE WITH CRANE STRUCTURE
Extended Crane structure with long stroke and 360° rotating capability
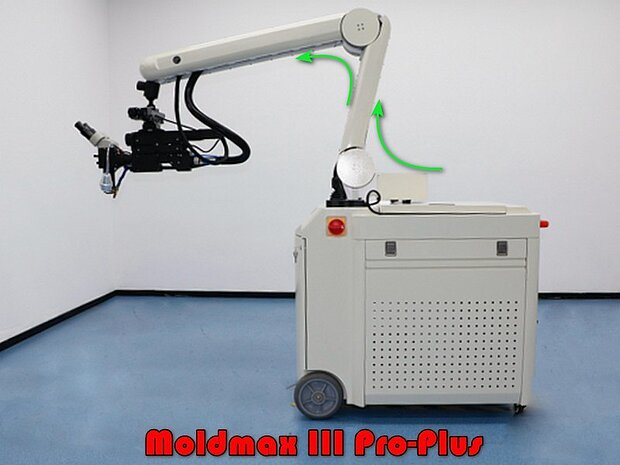
LW-MOLDMAX PRO+:
MOBILE MOULD LASER WELDING MACHINE WITH FOLDABLE AND RETRACTABLE BOOM
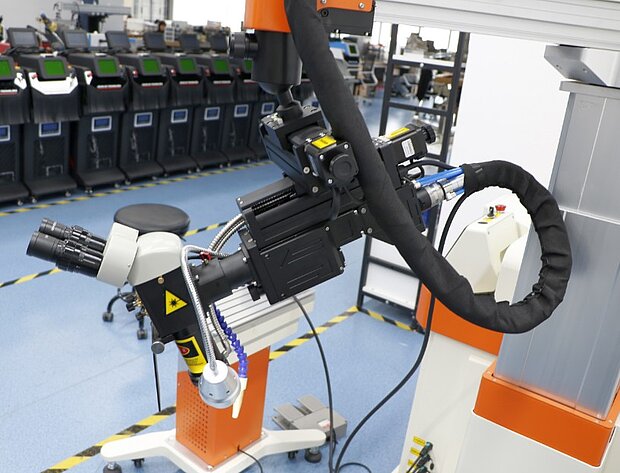
PREDEFINEd PRECISON WITH MOLDMAX MOLD LASER WELDING MACHINE
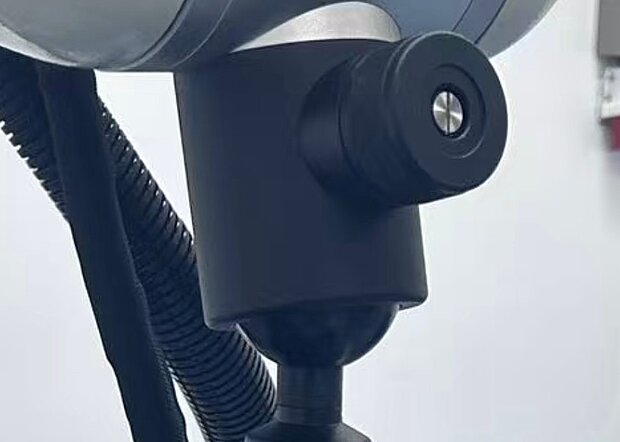
ROBOTIC ARM AND CARDAN SHAFT CONTROL
·The end of the robot arm is equipped with a universal shaft connector, which can manually control the welding head to rotate 360° to any angle and fix it, and the xyz axis can be electrically controlled to achieve a larger welding range. At the same time, with the help of an electric handle, the forward and backward, up and down movement of the robot arm can be fixed at the desired position to complete the process operation.
PRECISION AT YOUR FINGERTIPS! XYZ - AXIS
Three-axis joystick control axis system is used to accurately position the laser head and move it during operation
Our Moldmax III Pro laser welders all feature intuitive joystick control, designed for ultimate ease of use. With a single toggle for X, Y, and Z-axis movement, plus rotary control, the advanced joystick makes operating your laser system feel like second nature, letting you focus on the task, not the controls. Get ready for: Faster setups + Smoother operation + Unmatched accuracy
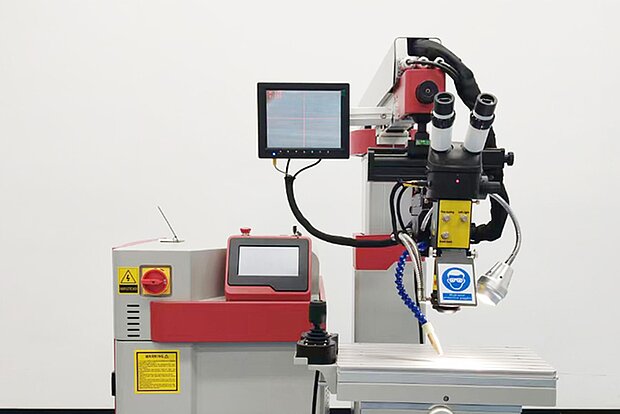
CCD CAMERA SYSTEM( OPTIONAL)
CCD camera can help you easy to view weld result and adjust exact weld position.
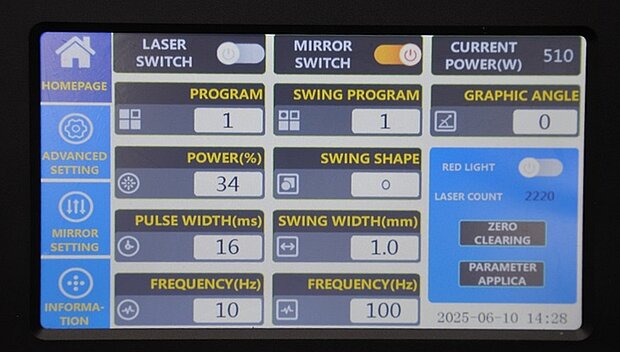
EASY TO SET UP PARAMETER OF CONTROL SYSTEM
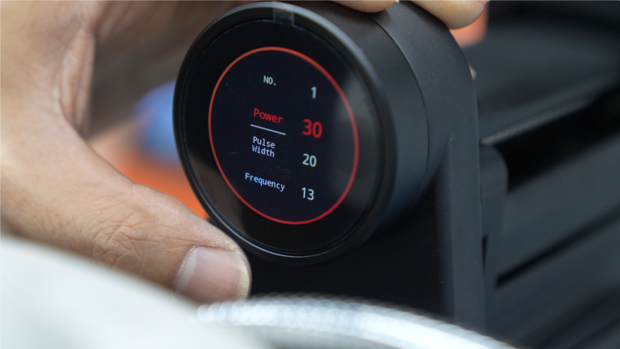
ADDITIONAL CIRCULAR PARAMETER ADJUSTMENT TURNING KNOB WITH SCREEN
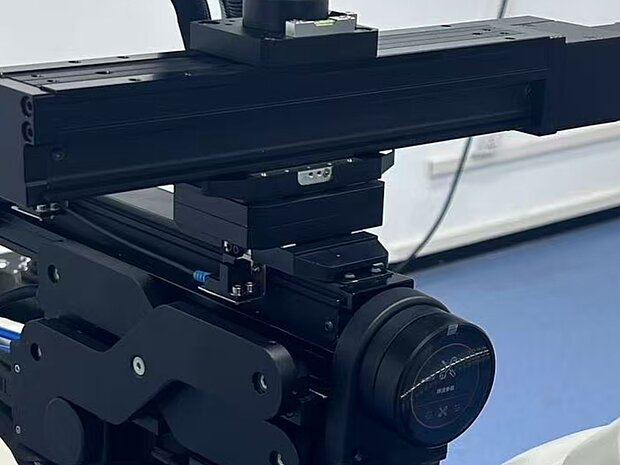