Hardfacing is a group of welding related technologies, also known as cladding or overlaying.
Hardfacing protects or restores the surfaces of equipment and parts,
extending their working life by applying a hard and wear resistant material.
Hardfacing increases the lifespan of your products by up to 800%
For severe abrasion, the Tungsten Carbide Embedding hardfacing process offers the ultimate in wear and abrasion protection and is extremely impact resistant.
Tungsten Carbide particles are delivered to a molten weld pool at precisely the right moment prior to the puddle freezing.
The result is a 60Rc tool steel matrix weld deposit filled with Tungsten Carbide grit.
Used in a number of industrial applications Tungsten Carbide is characterized by its high strength, toughness, and hardness.
What’s the Difference Between Hardfacing and Cladding?
“Hardfacing” and “cladding” are two terms that are often used synonymously, not realizing they are distinctly different applications. If so, you are in good company, as it is a common misconception. Hardfacing is a welding process that applies a high-wear surface to add protection and extend the life of the object. The material welded typically contains carbides and, in most cases, this is tungsten carbide [WC]. Cladding, however, will typically use overlay material that is similar to the base material but in many cases uses a different material to give a beneficial property to just that portion of the component, such a high hardness, corrosion resistance, or just to meet a refurbishing function. As with cladding, laser hardfacing cannot be machined and must be ground.
Hardfacing vs. Cladding Process
Though hardfacing and cladding are surface overlay processes that are different only in material characteristics that meet different requirements, they both can be achieved using similar processes:
- Lasers
- Thermal spray
- Flux-cored arc welding or FCAW
- Plasma Transfer Arc [PTA] welding
The choice between hardfacing and cladding comes down to the characteristics you want to impart, the materials involved, and an understanding of the environment that the surface is subjected too. In hardfacing, the heavy, wear-resistant carbide/metal deposit can be applied by laser, thermal spraying, spray-fuse, or welding. Thermal spraying is best for items sensitive to heat distortion, as opposed to spray-fuse that requires flame spraying and fusion with a torch. Thermal spray is not a welding process; therefore, bond strength is very low as compared to a welded or brazed overlay. Traditional weld hardfacing can be used to apply a very thick layer (up to 10’s of mm) of wear-resistant material. Laser hardfacing has benefits over the other processes primarily because it is a welding process that has lower heat, lower dilution, and less dissolution of the carbide. This all enables the ability to achieve very thin hardfacing overlays.
Cladding is a weld overlay process yielding an entirely new surface that can be used with a large variety of overlay materials in different forms such as powder, wire, or cored wire. Again, traditional overlay processes can be used as listed above. Just like laser hardfacing, laser cladding has benefits over the other processes primarily because it is a welding process that has lower heat and lower dilution. This all enables the ability to achieve very thin clad overlays.
Laser hardfacing and cladding are used in almost every industry market with applications such as:
- Oil and gas
- Automotive
- Construction equipment
- Agriculture
- Mining
- Military
- Energy generation
- Repair and refurbishment of tools, turbine blades, and engines
Laser hardfacing and laser cladding both provide the advantages of little thermal distortion, high-productivity, and cost effectiveness.
Laser Hardfacing
Use of Lasers in Hardfacing and Cladding Processes
Fiber laser hardfacing is a welding overlay process that is applied to the material handling components to resist wear and prolong life; It is a unique laser cladding process that can apply a thin layer of welded metal with embedded super-hard particles producing extreme wear resistant coatings. This inherently low heat process produces low distortion, smoother, thinner and more uniform anti-wear coatings as compared to any other welding process. The lower heat does not burn out the carbides, achieving hard particle densities up to 75%. Using lasers as a heat source in hardfacing and cladding provides precision and the lowest amount of chemical dilution to weld two materials. It offers a cost-effective way to use less expensive substrate materials by applying a weld overlay, which provides the corrosion, oxidation, wear, and temperature resistance. The high production rate with which products can be completed combined with material cost advantages make laser cladding and hardfacing a popular choice for many industries.
Tungsten Carbide Laser Hardfacing
Tungsten carbide is the standard for high performance hardfacing. There are several reasons, beside hardness that Tungsten carbide is the hardfacing ceramic of choice, it is very chemically stable at molten metal temperatures and not as reactive as is the case with diamond [carbon]; it is has a very high density as compared to silicon carbide, titanium carbide, which means that it will not float on the molten metal.
Applications
- Metal components experiencing high intensity wear such as ground, rock, dust or sand engagement devices
- Down hole component for oil & gas– mud pump components
- Coal and ash handling equipment
Benefits
- Low heat input
- Fast cooling
- Negligible disassociation of carbides
- Stress free overlays
- Higher hardness
- Fine microstructure
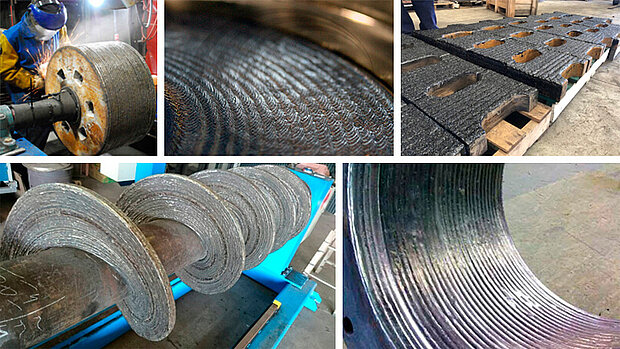
Laserweld Overlay, Lasercladding with wire, and Laser Hardfacing
Layer Build-up with Laser and welding wire
When it comes to industrial applications, equipment is often subjected to harsh conditions that can cause wear, corrosion, and other forms of damage. To protect these components and extend their useful life, various techniques are used to add a layer of material to the surface, creating a barrier between the equipment and the environment.
Three of the most common techniques used for this purpose are Weld Overlay, Cladding, and Hardfacing.
- Weld Overlay or Laser Metal Deposition with Wire involves adding a layer of material to the base metal through welding, which can improve the metal’s resistance to wear, corrosion, and other types of damage.
- Cladding, on the other hand, involves bonding a layer metal powder of one material to another to enhance the properties of the base material.
Hardfacing or is a type of weld overlay that involves adding a layer of hard, wear-resistant material to protect against abrasion, impact, and erosion.
While all three of these techniques can be effective in certain situations, each has its own strengths and weaknesses.
WELD OVERLAY
Laser Weld Overlay or Laser Metal Deposition with Wire
Definition and explanation of the technique
Weld Overlay is a technique used in welding and metallurgy to add a layer of material to the surface of a metal substrate. The layer can be made of the same material as the base metal or a different one, and it is applied using welding techniques such as gas tungsten arc welding (GTAW), shielded metal arc welding (SMAW), or gas metal arc welding (GMAW). Now Lasermach has developed the new laser welding overlay technology .
The New Laser Weld Overlay process involves melting a filler material under the forme of one or more wires and depositing it onto the surface of the substrate. The filler material is chosen based on the specific properties needed for the application, such as resistance to wear, corrosion, or high temperatures. Once the filler material is deposited onto the substrate, it cools and solidifies, creating a layer that is bonded to the substrate.
Advantages and disadvantages
One advantage of Weld Overlay is that it allows for the addition of a protective layer to a surface without requiring the entire component to be replaced. This can be a cost-effective solution for repairing damaged or worn parts, as it can extend the life of the component and avoid the need for expensive replacements. Weld Overlay can also be used to modify the surface properties of a component, such as increasing its hardness or improving its wear resistance.
However, Weld Overlay also has some disadvantages. One potential issue is that the layer may not bond properly to the substrate if the welding process is not carried out correctly, leading to a weak or brittle layer that can fail prematurely. In addition, Weld Overlay can add stress to the component, which may cause cracking or other forms of damage over time.
Weld Overlay has many applications in industry, including the repair of worn or damaged components in machinery, the creation of wear-resistant coatings on tools and equipment, and the modification of surface properties to improve performance in high-stress environments. It is also commonly used in the oil and gas industry to protect piping and other equipment from corrosion caused by harsh environments.
Overall, Laser Weld Overlay is a versatile and useful technique that can be used in a wide range of applications. However, it is important to carefully consider the specific properties needed for the application and to ensure that the welding process is carried out correctly to avoid potential issues with bonding and stress or dilletation of the surface material
CLADDING
Cladding
Definition and explanation of the technique
Cladding is a technique used in metallurgy to add a layer of material to a substrate. Unlike Weld Overlay, which involves melting a filler material and depositing it onto the surface of the substrate, Cladding involves bonding a layer of one material to another to enhance the properties of the base material. The two materials are typically chosen for their different properties, such as hardness, corrosion resistance, or thermal conductivity.
There are several ways to apply Cladding, but one common method involves using a rolling mill to bond the two materials together. The two materials are first cleaned and prepared, and then they are heated and rolled together under high pressure. The result is a strong, durable bond between the two materials.
Advantages and disadvantages
One of the advantages of Cladding is that it allows for the creation of a layer with specific properties that are different from those of the base material. This can be useful in a wide range of applications, such as improving the corrosion resistance of a metal component or enhancing its wear resistance. Cladding can also be used to create a composite material with a unique combination of properties that cannot be achieved with a single material.
However, Cladding also has some disadvantages. One potential issue is that the bond between the two materials may not be as strong as desired, which can lead to delamination or separation over time. In addition, the process of Cladding can be more complex and time-consuming than other techniques, which can increase costs and production times.
Cladding has many applications in industry, including the creation of corrosion-resistant materials for the chemical and oil and gas industries, the production of wear-resistant coatings for cutting tools and other equipment, and the manufacture of heat exchangers and other components that require specific properties. Cladding can also be used in architectural applications to create decorative or functional surfaces, such as metal façades or roofing.
Overall, Cladding is a powerful technique that can be used to enhance the properties of metal components and create new materials with unique properties. However, it is important to carefully consider the specific requirements of the application and to ensure that the Cladding process is carried out correctly to avoid potential issues with delamination or separation.
HARDFACING
Hardfacing
Definition and explanation of the technique
Hardfacing is a technique used in metallurgy to increase the hardness and wear resistance of metal components. It involves applying a layer of hard, wear-resistant material to the surface of a substrate, typically using a welding process. The layer is chosen based on the specific requirements of the application, such as resistance to wear, abrasion, or impact.
The Hardfacing process involves melting a filler material and depositing it onto the surface of the substrate. The filler material is typically a harder, wear-resistant material than the base metal, such as tungsten carbide, chromium carbide, or a ceramic material. The Hardfacing layer is then bonded to the substrate using a welding process such as gas tungsten arc welding (GTAW), shielded metal arc welding (SMAW), or gas metal arc welding (GMAW).
Advantages and disadvantages
One of the advantages of Hardfacing is that it can significantly extend the life of metal components that are subject to wear and abrasion. By adding a layer of hard, wear-resistant material to the surface of the component, Hardfacing can reduce the rate of wear and prevent premature failure. Hardfacing can also be used to repair damaged components, such as worn or chipped gears or worn-out hydraulic components, by restoring their original dimensions and properties.
However, Hardfacing also has some disadvantages. One potential issue is that the Hardfacing layer may not bond properly to the substrate if the welding process is not carried out correctly, leading to a weak or brittle layer that can fail prematurely. In addition, the Hardfacing process can add stress to the component, which may cause cracking or other forms of damage over time.
Hardfacing has many applications in industry, including the manufacture of mining equipment, agricultural machinery, and construction equipment. It is also commonly used in the oil and gas industry to protect drilling tools and other equipment from wear caused by harsh environments. Hardfacing can also be used in the aerospace industry to improve the wear resistance of turbine blades and other components subjected to high temperatures and high stresses.
Overall, Hardfacing is a powerful technique that can significantly extend the life of metal components subject to wear and abrasion. However, it is important to carefully consider the specific requirements of the application and to ensure that the welding process is carried out correctly to avoid potential issues with bonding and stress.
Comparison of the 3 Techniques
Weld overlay - Cladding - Hardfacing
When it comes to improving the performance and lifespan of metal components, three common techniques are weld overlay, cladding, and hardfacing. Each technique has its own unique advantages and disadvantages, and choosing the best one for a particular application requires careful consideration of factors such as the specific requirements of the component, the environment in which it will be used, and the available resources.
Weld overlay involves depositing a layer of metal onto the surface of a substrate to improve its resistance to wear, corrosion, or other forms of damage. The advantages of weld overlay include its versatility, which allows it to be used on a wide range of components and applications, and its ability to provide a relatively thick layer of protection. However, weld overlay can be difficult to apply accurately, which can lead to inconsistencies in the thickness and quality of the overlay. It also requires significant expertise and experience to perform properly.
Cladding involves adding a layer of material to the surface of a substrate to provide protection and insulation. Common cladding materials include brick, stone, metal, and glass. The advantages of cladding include its ability to provide excellent protection against weather and other environmental factors, as well as its versatility and aesthetic appeal. However, cladding can be expensive and time-consuming to install, and it may not be suitable for applications where weight or thickness are concerns.
Hardfacing involves applying a layer of hard, wear-resistant material onto the surface of a metal component to increase its resistance to wear, abrasion, or impact. The advantages of hardfacing include its ability to provide excellent protection against wear and tear, as well as its versatility and relatively low cost. However, hardfacing can be difficult to apply accurately, which can lead to inconsistencies in the thickness and quality of the overlay. It also requires significant expertise and experience to perform properly.
Choosing the Best Technique for Your Application The choice of welding technique depends on the specific requirements of the application, including the type of metal component, the environment in which it will be used, and the available resources. For example, if the component is subject to heavy wear and tear, hardfacing may be the best choice.
Conclusion
In conclusion, Weld Overlay, Cladding, and Hardfacing are all effective methods for improving the surface properties of materials. Weld Overlay involves depositing a layer of material onto the surface of a base metal, while Cladding involves bonding a thin layer of material onto the base metal. Hardfacing involves depositing a layer of hard and wear-resistant material onto a base metal. Each method has its own advantages and disadvantages, and the choice of method will depend on the specific application and the desired properties of the surface. Weld Overlay and Cladding are often used to provide corrosion resistance, while Hardfacing is used to increase wear resistance. Ultimately, the choice of method will depend on the specific requirements of the application and the available resources.
Laser wire buildup welding (LDA)
particularly economical, clean and rework is reduced to a minimum.
At the process Laser wire buildup welding (LDA) the laser beam melts the wire and the base material, the melt bonds firmly and solidifies again until a small bump remains.
When the individual welding paths overlap precisely, the desired shape is gradually applied.
Areas of application of laser buildup welding with wire are the Repair components as well as the Functionalizing surfaces.
The process is particularly economical, clean and rework is reduced to a minimum.
Different welding wires are available as additional material.
So it is possible, homogeneous material or to create functional layers according to the coating requirements.
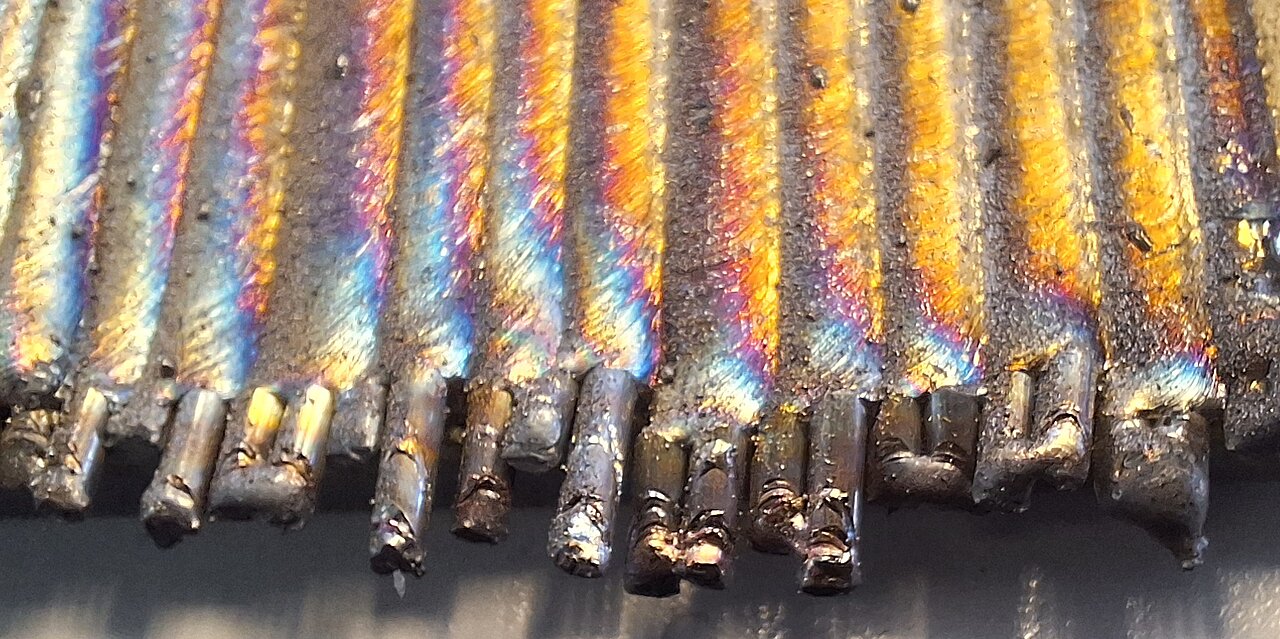
High speed Layer Build-up with Wire, double wire or triple wire
Cladding at laser speed till 40 times faster
Laser wire cladding
The laser beam connects the metal workpiece with the molten wire that is applied. Various steels, cast iron, copper, aluminum, nickel-based and cobalt-based alloys can be used as the base material. The layers are formed from iron-based alloys (low-alloy steels, tool steels, stainless steels), nickel-based alloys such as Inconel (625, 718, 738), cobalt-based alloys such as stellites, high-temperature alloys, aluminum alloys, titanium alloys and materials containing carbides, to offer additional wear protection. The decisive factor is the availability of the filler material in powder form, with a typical particle size of 40-120 µm, to enable the use of a coaxial powder nozzle is completely solved when using our new laserwire cladding technology. diode lasers achieve excellent results when melting metal powder: excellent adhesion, high precision, virtually no porosity and limited cracking with a high degree of hardness and minimal deformation. In most cases, the surface that results from the mixing does not require any further machining. Conventional hard facing processes, such as plasma powder deposition welding, on the other hand, do not achieve a sufficiently long service life for many applications.
Laser Metal Deposition with Wire by hand or automatic
In this process, the laser beam melts the wire that is fed in and the material of the component to be coated. Wire with diameters of approx. 0.8 to 2.0 mm is used, which is led to the additive welding process by commercially available wire feeders. Dual wire feeding is also available which doubless the production output and redusces the cost drastically. Today, it is estimated that 90% of the applications involve being coated with powder and 10% with wire but with our new solution, this will surely change drastically soon.. Areas of application for laser deposition welding with wire include the repair of components and the functionalization of surfaces. The process is particularly economical and clean, this without any manterial losses, low energy input and high speed and reworking is reduced to a strict minimum.
Our laser wire Cladding Machines
"HARD-Master" Series
Available in 09/2025
Roller Repairing by Hardfacing with Wires
Vertical Roller Hardfacing laser welding Suitable for repairing coal grinding mill, grinding disc, cement vertical mill, etc.
Squeeze Roller Hardfacing laser welding Suitable for base layer,buffer layer and pattern layer