Because of the need for high productivity and weld quality, the industry has readily adopted Laser Wobble Welding, which includes applications for seaming, sealing, and welding of body structures, as well as welding of transmission components.
Fiber Laser Welding Solutions Are Everywhere With Much More To Come Every Day
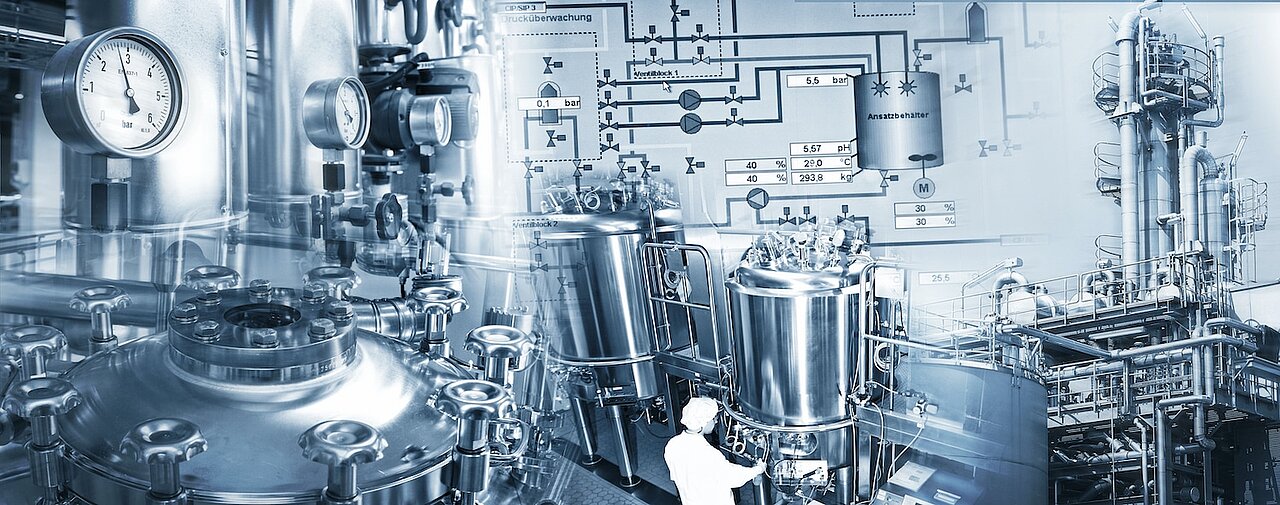
Fiber Laser Welding Solutions Are Everywhere With More Coming
Fiber Laser Wobble Welding Solutions Are Even opening Much More Doors
Laser welding shouldn’t be considered ‘nontraditional’ given the many applications over many years. Now with fiber laser welding, and specific with fiber laser wobble welding, new product applications are everywhere – in electronic packages, medical devices, the vehicles we drive, the aircraft in which we fly, in process equipment and sensors. The list is almost endless. Most of the earlier limitations of laser welding no longer exist or are easily overcome.
While fiber laser welding may at first be intimidating, it has been repeatedly demonstrated to enable new product designs with significant improvements in cost, quality and performance. Laser system suppliers, with available applications engineering staff, now provide turnkey solutions. That includes not only the machine but also fixturing and easily learned processing techniques.
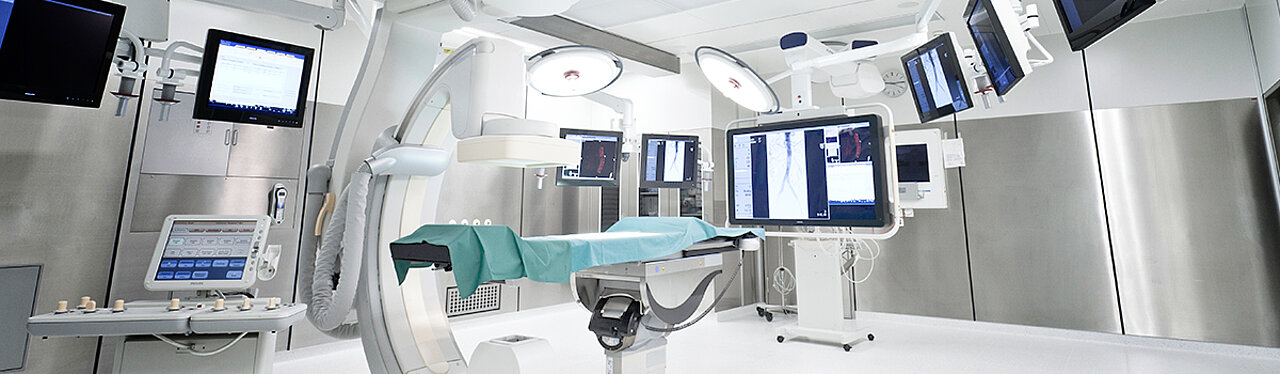
Medical Industry
Products within the medical industry require the highest levels of precision. You have to meet the highest quality demands. The size of many medical devices and products is continually decreasing, and lasers are perfectly suited for creating equally minute weld seams. Even in complicated areas, laser weld spots and seams can easily be generated to provide sterile surfaces with no post-processing.
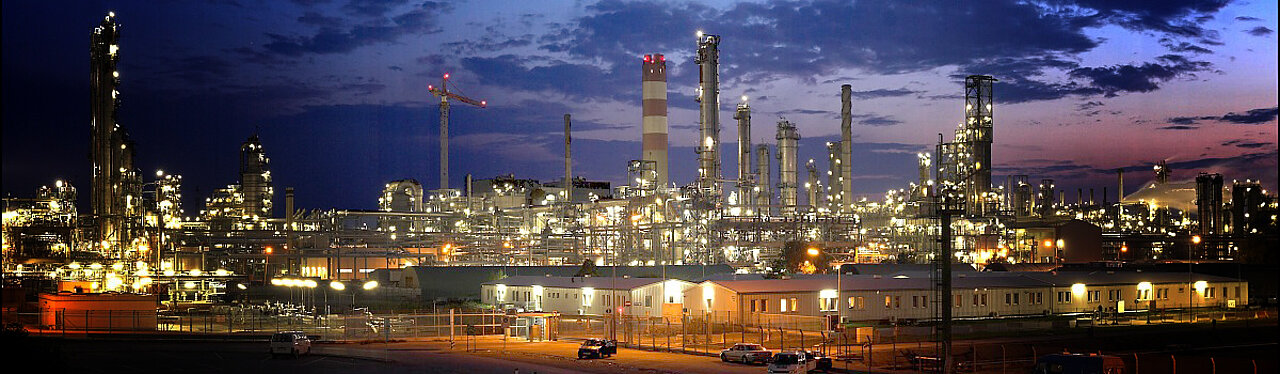
Gas and Oil Industry Repairs by Laser Welding
With Laser welding Technology rapidly customers within the Oil and Gas industry, changing over to laser welding services for both repairs, modifications and concept work. the result is faster, better and cheaper.
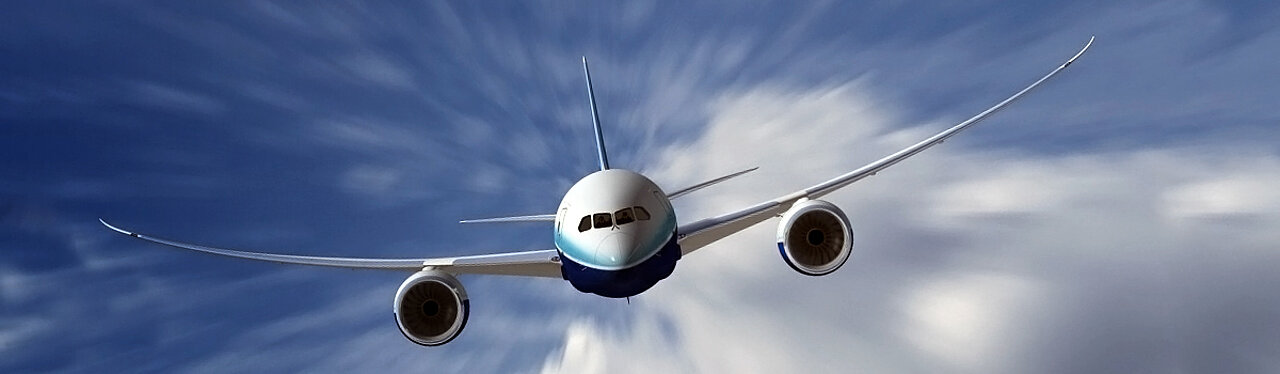
Aerospace Industry
The capabilities of laser welding have proven to play an integral role in the production of aerospace materials and parts. Examples of this would be in airport security procedures or flight components. The need for maximum precision leaves no room for error and laser welding offers high levels of accuracy. Therefore, making it a favourable technique for an excellent standard of work that meets specifications and regulations.
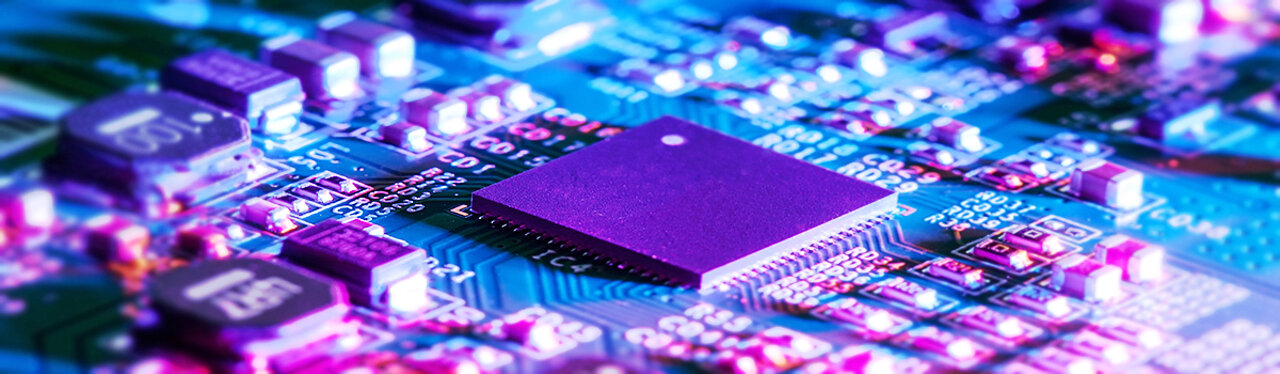
Hermetic Laser Welding of Electronic Packages
Hermetic sealing electronics in medical devices, such as pacemakers, and other electronic products has made fiber laser welding the process of choice for applications requiring the highest reliability. A recent advance in the hermetic welding process has addressed concerns about laser welding and the end point of the weld, a critical location point in completing the hermetic seal. Previous laser welding techniques resulted in a depression at the end point when the laser beam is turned off, even when ramping down the laser power. Advanced control of the laser beam eliminates the depression in both thin and deep penetration welds. The result is consistent geometry and lack of porosity at the end point with improved cosmetic appearance and more reliable hermeticity.
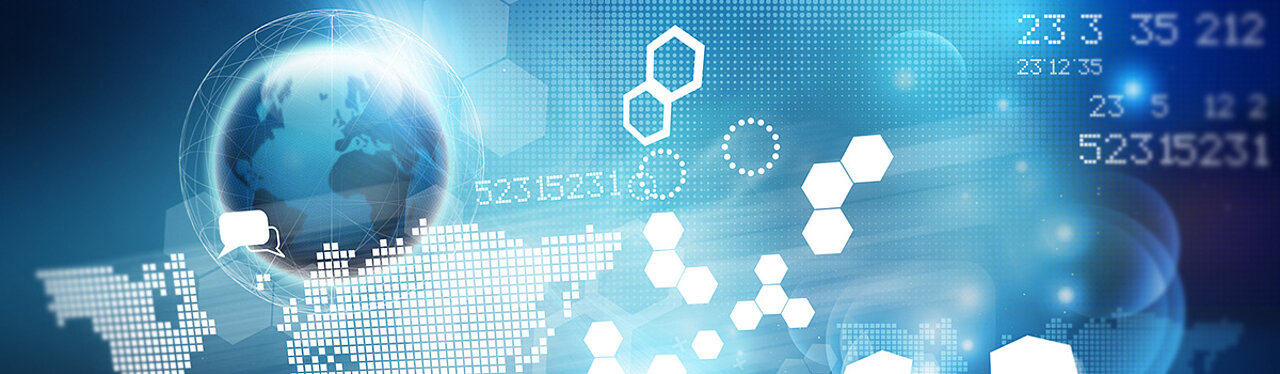
Aerospace Welding
Fiber laser welding high temperature nickel-based aerospace components ensures a consistent and robust joint. Welds that meet the geometry and quality requirements for aerospace applications are readily produced.
Laser welding nickel and titanium-based aerospace alloys requires control of the weld geometry and weld microstructure, including minimizing porosity and controlling grain size. In many aerospace applications, the fatigue properties of the weld are a critical design criteria. For this reason, designers nearly always specify that the weld surfaces be convex, or slightly crowned, to create a reinforcement of the weld.
To achieve this, a 1.2 mm diameter filler wire is used in the automated process or you use a wobble welding head. Addition of the filler wire to a butt joint leads to a consistent crown on both the top and bottom weld bead. The selection of the alloy of the wire also contributes to the weld’s mechanical properties by ensuring a sound microstructure of the weld.
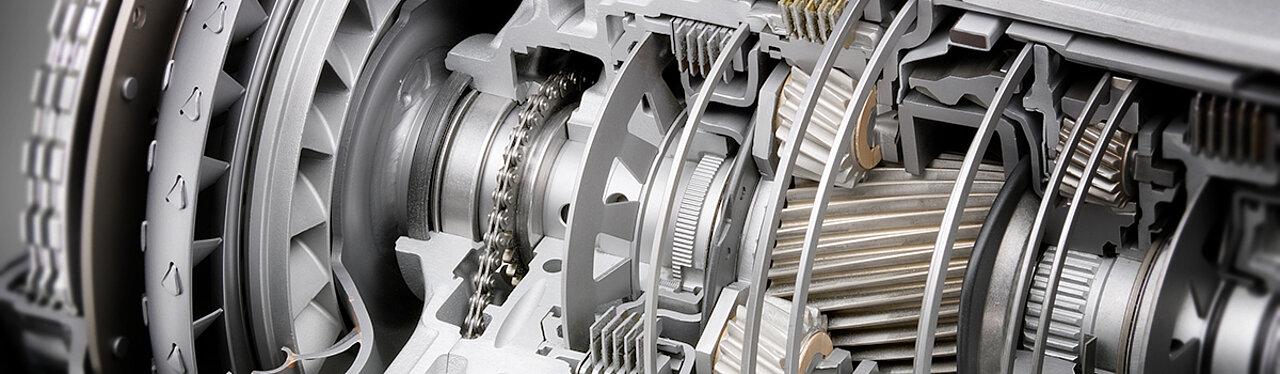
Laser Welding in Precision Machined Component Welding
Seals used in ships and chemical refineries and for pharmaceutical manufacturing were originally TIG welded. Because of their use in sensitive environments, these components are precision machined and ground from high temperature and chemical resistant nickel-based alloy material. Lot sizes are usually small and the number of setups are many.
The assembly of these components has been improved using fiber laser welding.
Justification to replace the earlier robotic arc welding process with fiber laser welding using a four axis cartesian coordinate machine tool were:
- consistently higher quality of the laser welds,
- ease of changeover from one component configuration to another that reduced setup time,
- automating the laser welding process using a four-axis CNC laser machine improved throughput while decreasing assembly costs.
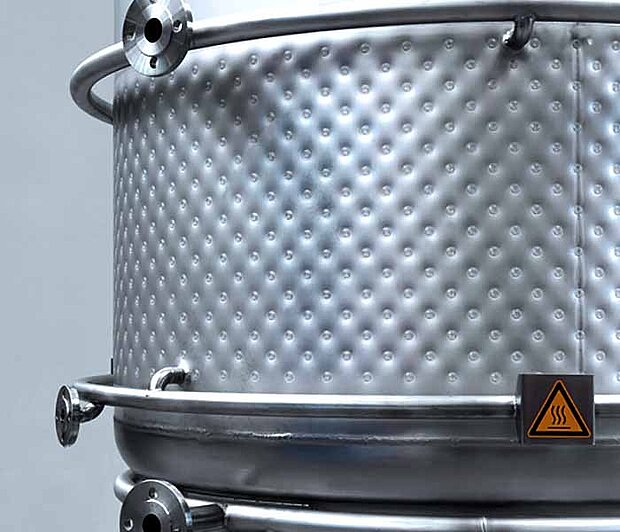
Laser Welding in Food and Beverage Industry
You must have a high-quality weld and surface finish within the food and beverage industry, due to the hygienic requirements. If the weld integrity or surface finish isn’t perfect and faultless, the consequences could be both expensive and unsanitary. Even the smallest niche left by a weld can allow the product to get trapped and form bacteria which could potentially contaminate the food.