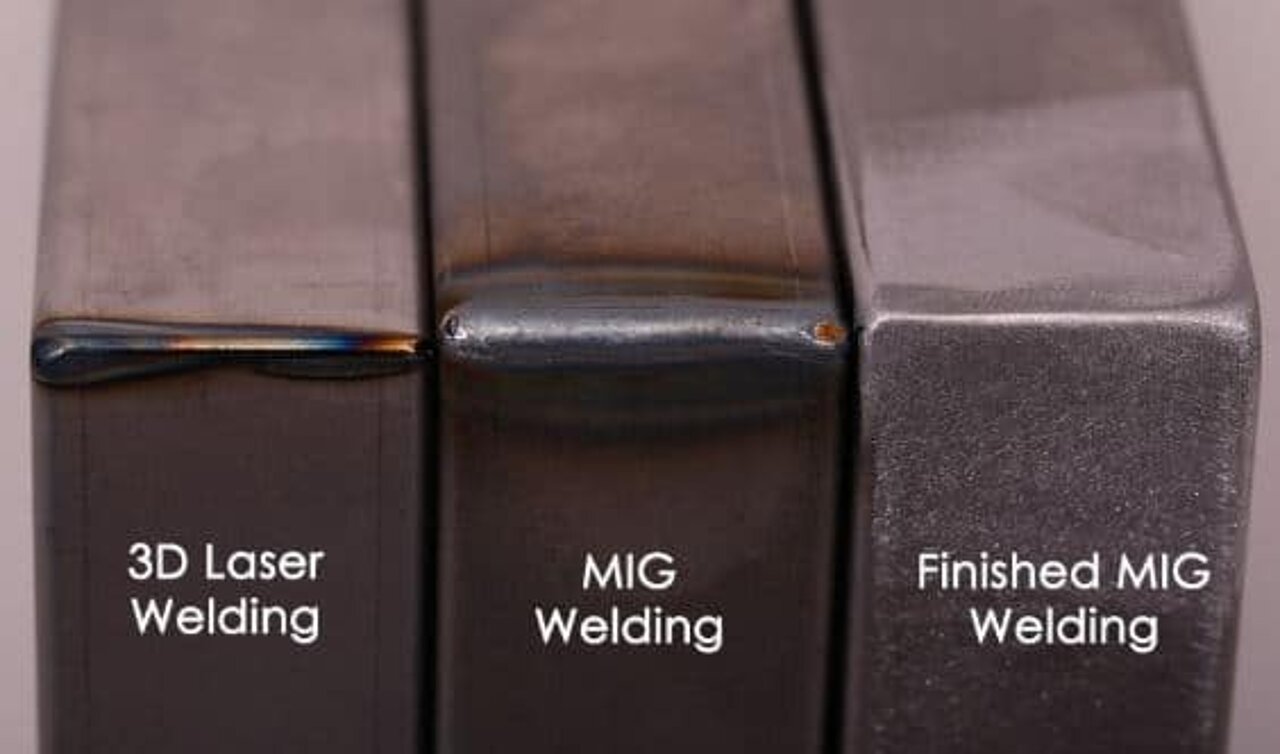
The Advantages of Laser Welding Over Arc Welding
Product designers and process engineers considering laser welding as an alternative to more conventional types of welding, such as MIG-MAG or/and TIG arc welding, will find each has its plusses and minuses. But for most applications laser welding is a cleaner, more precise, and more controlled method of welding and is especially much faster and better controllable.
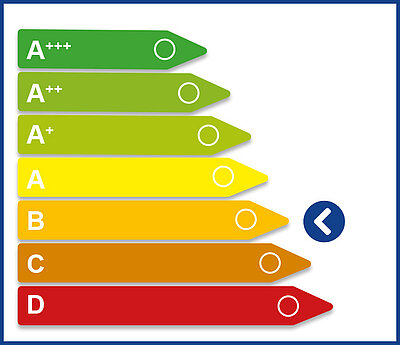
Metal Arc Welding
Class B
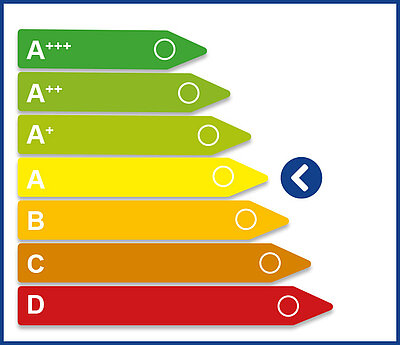
Plasma Beam Welding
Class A
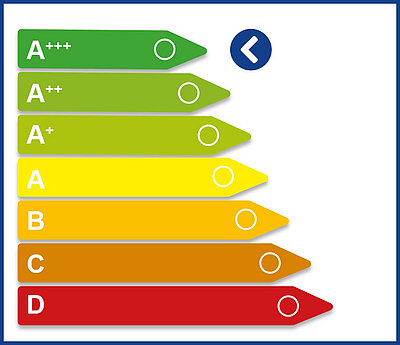
PhotonWeld
CLASS A+++
Add the best energy saving technology for lasers to "the" best laser welding machines
PhotonWeld© = Class A+++
Energy saving has become a priority for welding industry. This is due to the recent increase in energy demand and constraints in carbon emissions. Increasing environmental demands from governmental and customers strain the importance of reducing the environmental pollution while welding. Therefore, the minimum energy-oriented green welding process is must. Wobble Laser Welding (WLW) is considered to be the most significant development in metal joining and is a “green” technology due to its energy efficiency, environment friendliness, increased speed, reduced postprocessing and cleaning, and versatility. As compared to the conventional welding methods, WLW consumes considerably less energy. Add to this the revolutionary EcolEner energy saving technology based on 976nm pumping technology, and nobody can beat us anymore in energy saving.
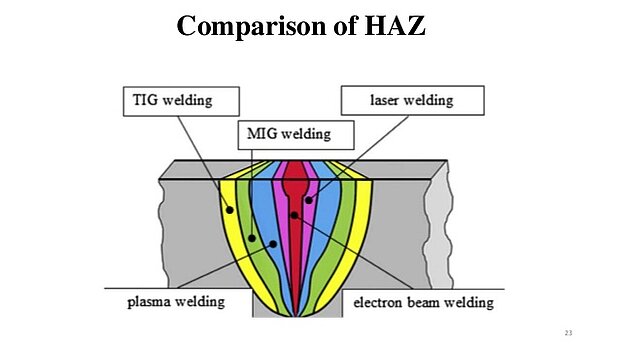
Due to the small spot size of the laser, the heat input is typically 200 times lower than with MIG, TIG or arc welding processes.
Due to this VERY HIGH Concentrated Heat input, our Wobble Laser Welding Machines create almost NO Heat Affected Zone (HAZ) resulting in almost NO deformation of the workpiece.
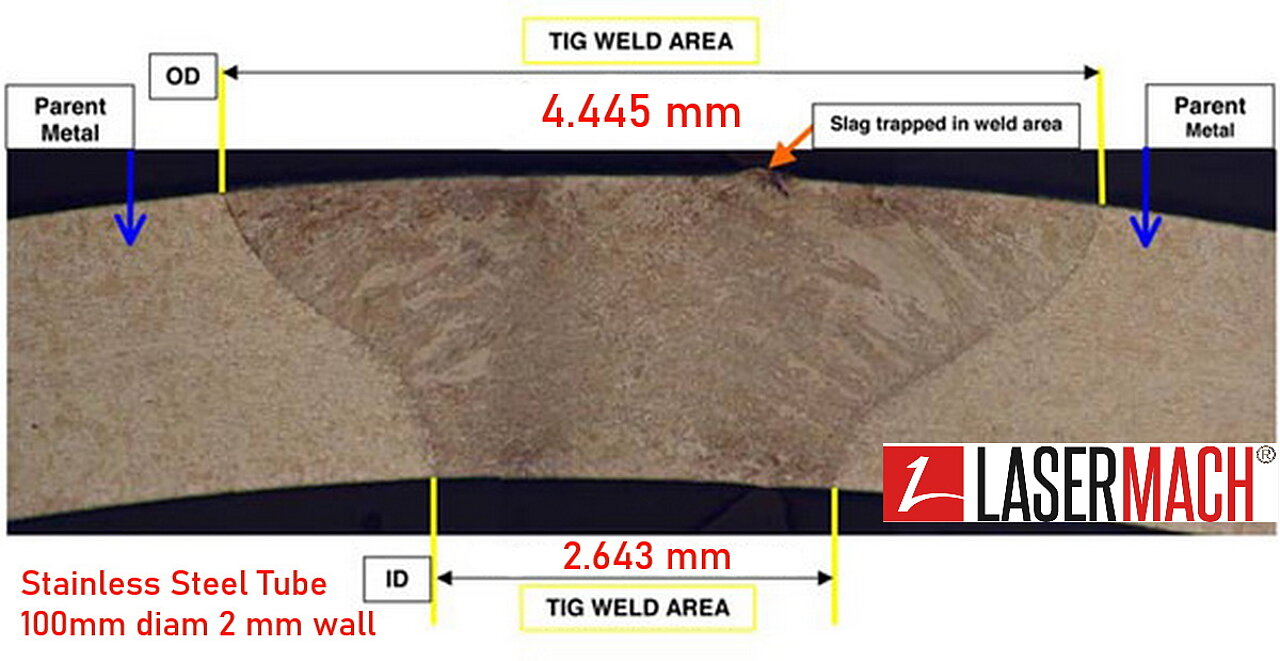
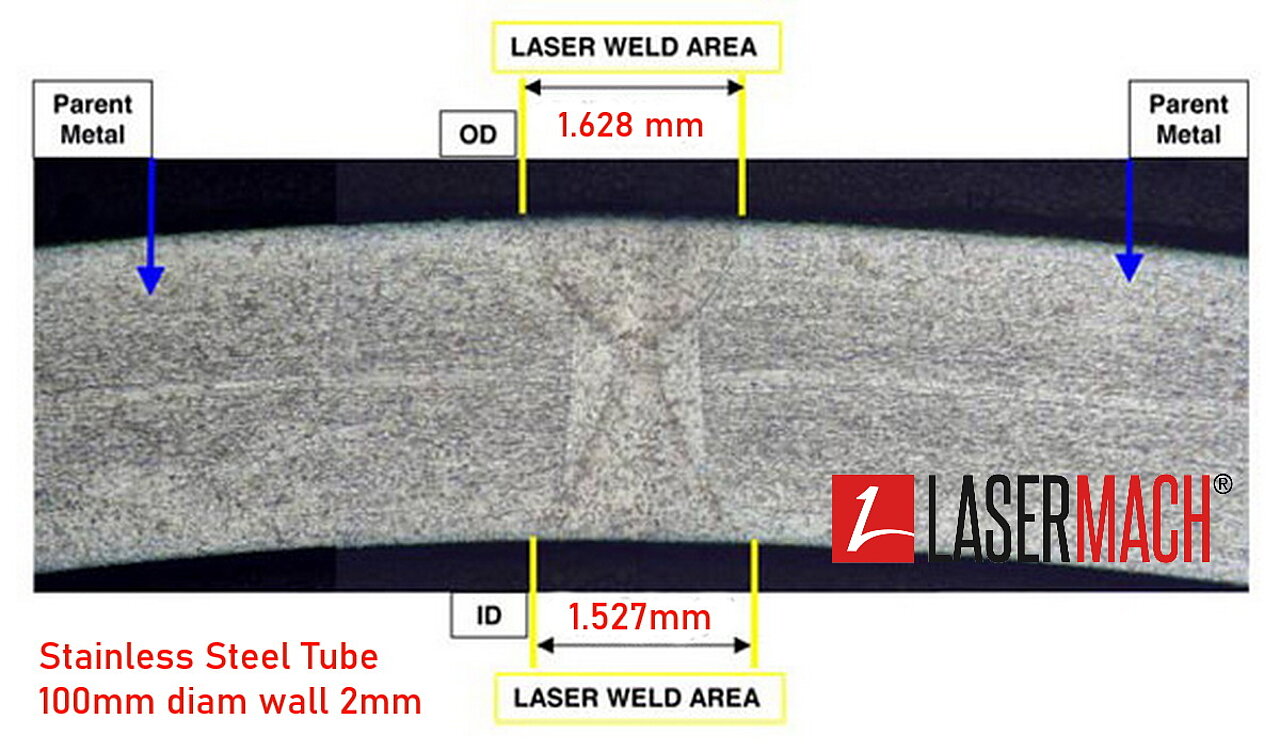
Laser welding Versus Arc Welding
Before comparing the two methods in detail, it’s helpful to review how each of them works:
Before comparing the two methods in detail, it’s helpful to review how each of them works:
Laser Welding
In laser welding a laser beam is focused to a point usually just below the surface of the metals to be welded, causing the metals to heat and melt at the point of the weld. In their liquid state the two metals combine so that when they cool they are bonded. The laser beam has a high-power density (typically 10 MW/cm²) producing very small, Heat-Affected Zones or HAZ zones. These are typically fractions of a millimeter to a few millimeters in diameter and they heat and cool very rapidly.
ARC Welding
Say the word “welding” and most people will immediately think of a person holding an acetylene torch like the kind they may have used in high school shop class. Today’s industrial welding, however, is typically arc welding in which the heat source is an electric arc formed between an electrode and the base metals being welded. The two main types of arc welding are TIG and MIG.
In TIG (Tungsten Inert Gas) an inert gas flows around the electrode to protect the weld from contamination. In addition to the electrode the welder also holds a stick of filler (flux) that melts in the heat of the arc and that, when cooled, bonds the metals. Excess filler that solidifies around the weld, called slag, must then be removed, usually by grinding. As filler sticks are con- sumed during welding they are replaced.
MIG (Metal Inert Gas) is similar to TIG except that the electrode itself is composed of the filler material. The electrode is therefore consumed during welding and must be replaced when depleted.
Comparing Laser Welding to MIG and TIG Arc Welding
Types of material to be welded. Lasers can weld many types of materials together including many types of stainless steel, titanium, copper, and aluminum (although the two pieces being welded must be different kinds of aluminum). However, not all metal combinations are “bondable.” In conventional welding the metals don’t bond directly with each other but with the filler. So metal-to-metal compatibility is not an issue — which is why conventional welding can weld more types of metal than laser welding.
Material thickness. Laser welding is suitable for jobs ranging from as thin as 100µm up to about 8 mm (in the case of steel). That means that laser welding can be used for jobs where the metal is so thin that conventional welding would destroy it. On the other hand, conventional welding can easily handle large pieces — such as large pipes or structural beams in a building — that laser welding can’t.
Precision. The power output, size of weld, depth of weld, speed of weld, and the track of the laser beam on the metal surface are all highly controllable. The result is a very precise weld — you heat just what you want to heat to the degree you wish to heat it. Among other advantages versus conventional welding, there’s less likelihood of damaging or deforming the surrounding surfaces or components like electrical components that may already be installed.
Automation. Another benefit of a highly controlled process is that laser welding is highly programmable and robotic. Since it’s easier to automate compared to MIG or TIG welding methods, greater repeatability and faster throughput can be achieved.
Contamination. With laser welding, the only materials involved are the metals to be welded. For best results the metals must be cleaned of any oil and dirt prior to welding. The welding itself introduces no filler or slag that could contaminate application environments, such as an operating room in the case of surgical instruments.
Environmental impact. A cleaner process also means there’s much less impact on the environment.
Corrosion. With some metals such as steel, aluminum and titanium alloys, brittleness can result from conventional welding if the electrode used for welding contains traces of moisture. The heat of the welding causes the water to decompose and release hydrogen that enters the metal causing it to become brittle. This can’t happen with laser welding because there is no electrode.
CONCLUSION
The best way to compare laser welding to arc welding is on the basis of your own product and production requirements.
- Are you looking for a very precise weld?
- Do you require an intricate weld pattern or is the area to be welded difficult to reach?
- Is minimal cleanup, low contamination risk, and low environmental impact important?
- Do you need to integrate welding with other manufacturing steps — so automation and high repeatability are both key?
If you answered yes to any or all of these questions then you may wish to consider laser-welding, especially if the metals to be welded together are thin. One way to know for sure which method of welding is best is by discussing your application with our laser-welding expert first, before you commit to a process.
Call +32 (0)56333240 or male sales@photonweld.com