Laser Welding explained simple
What is laser light?
What is laser radiation?
Light: It travels at 299.792.458 meters per sec. Its visible spectrum ranges from 400 to 700 nanometers. Its smallest unit is a packet of energy, a photon. In most of its natural and artificial forms, light has little power.
However, a groundbreaking invention in the latter half of the 1950s increased its power and concentrated it in a small area. Thus was born a modern and revolutionary concept: LASER - Light Amplification by Stimulated Emission of Radiation
LASER: It is concentrated light of one single frequency or one single colour.
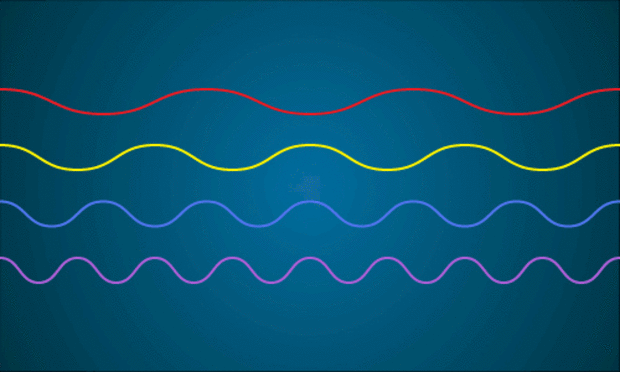
Light We See
Mixture of different frequencies of light and colour
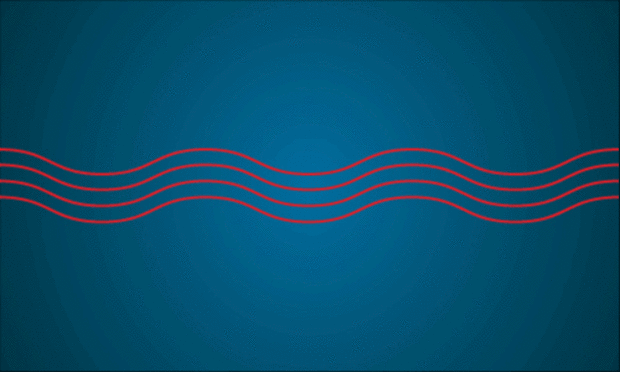
laser Light
Single frequency - single colour light beam
Laser Welding
INfrared Fiber laser welding, like other laser-machining methods, is a non-contact technology that has a limited, heat-affected zone (HAZ), which is why the technology is a preferred method for welding delicate and high tensile products at high speeds. Laser welding is also a more repeatable and consistent process than other welding methods, and is capable of producing high-strength bonds without the need for filler material, flux, prepping, or secondary cleaning and finishing processes. Laser Welding enables many applications to be manufactured at much lower costs, with greater consistency, at greater speeds, and with much less waste and quality-control issues. Moreover, a laser welding manufacturing process is much more reliable than other welding technologies, as the latest laser-welding machines require little to no maintenance, and virtually have no downtime.
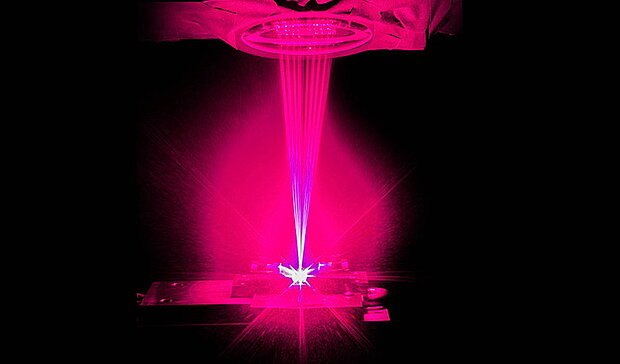
The laser as a heating source to weld metal
Laser welding requires that the laser raise the temperature of the material to be welded. The laser light must be absorbed by the material to induce a temperature rise. In effect, the laser light beam is focused onto the material similar to the way the sun can be focused by a magnifying glass. The difference is that the laser’s power density is many orders of magnitude higher.
Laser light photons (packets of light energy), impinge onto the material and are partly or wholly absorbed. The energy of the photon is absorbed in the metal material and causes a heat waves within the metal. Repeated absorption of photons eventually leads to metal melting.
Even for metals that absorb well, such as steel, the laser is initially mostly reflected. A smaller percentage of the laser beam is absorbed, heating the metal surface. The increased metal temperature increases the absorption of the laser light photons. This creates a snowball effect, in which the material is rapidly heated by the laser, leading to melting and formation of the weld.
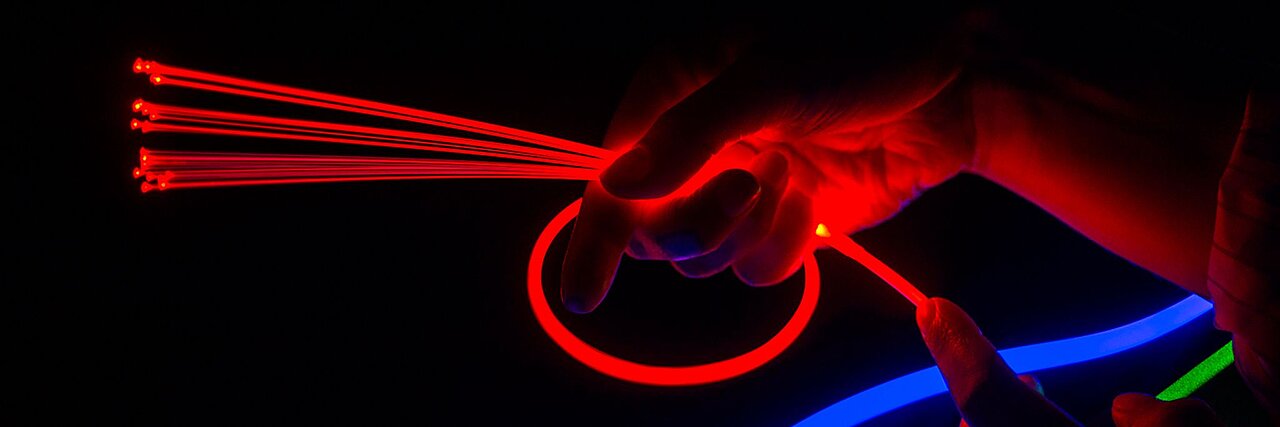
Fiber Laser Welding
Unlimited possibilities
Laser Welding is a welding technology used to join several metal components. A laser produces a beam of high-intensity that is concentrated into one spot. This concentrated heat source enables fine, deep welding and high welding speeds.
Traditional but old laser welding technologies, such as
- continuous-wave CO2 welding lasers are limited in terms of accuracy and undesired, high heat input into the weld and
- the traditional pulsed Nd:YAG welding lasers are limited by the maximum welding speed, the minimal spot size that can be achieved and the electrical to optical energy conversion efficiency that is very bad.
With the latest fiber laser welding, the output power and the oscillation form of the laser beam is possible to change. Fiber Laser Welding is also very suitable for welding materials with a high melting point or with high thermal conductivity due to a very low thermal effect during welding. The energy conversion rate is very high and all this makes fiber laser highly adaptable to various applications for use in various welding assembly processes.
The fiber laser beam used for welding can be adapted as follows and characterized by different laser oscillation modes :
Pulsed laser beam welding (PWM- Pulse Wide Modulation))
and
Continuous laser beam welding (CW - Continuous Wave)
Even more applications are demanding a higher precision control, lower heat input and lower electrical energy consumption.
Fiber Laser Welding is a technology that offers optimal solution for both: spot welding AND Seam Welding.
Is Laser Welding a Good Fit for Your Operation?
If you are looking to improve productivity and reduce costs in the welding operation, laser welding is one option to consider.
Laser welding is more accessible and affordable than ever — offering much faster travel speeds than other welding processes and weld consistency in automated and manual welding applications.
Improve productivity and save money
Finding ways to improve productivity and save money are important factors in any welding application. Companies often look at technology advancements to achieve these goals, but many operations might not consider laser welding — perhaps viewing it as too expensive or complicated.
Developments in laser welding technology have made it more accessible and affordable than ever. The process also offers significant productivity benefits that can deliver a fast return on investment. It’s especially well-suited for sheet metal welding applications.
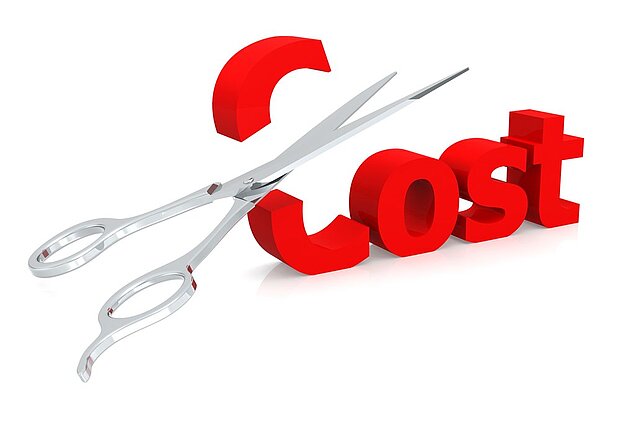
Laser welding does not operate on the same principles as other types of welding like TIG, MIG, MAG,..
Laser welding uses a beam of light, instead of electricity, to join two pieces of metal together through a superfast melting and cooling process.
Another key difference with laser welding is the intensity and ability to focus the heat source: the laser. The much higher, focused heat than, say, the electricity of a MIG welder or TIG welder, means that the weld occurs much more quickly. What’s more, the ability to narrowly pinpoint the weld area leads to much greater precision and more accurate and attractive weld joints.
What does this mean for you?
- Higher speeds: till 10x faster than MIG welding, and till 40x faster than TIG welding.
- Minimal/no finishing: The accuracy of the laser welding process means that little to no grinding or finishing is needed.
- Visually superior: Laser welding is ideal for straight line joints in furniture and other consumer products, since there is a much smaller heat-affected zone and a much tighter weld.
- Greater strength: A smaller heat-affected zone also means less weakening of the material.
So when wouldn’t you want to use laser welding? Thicker materials and parts where the weld joint construction does not allow the fit-up to be consistently maintained generally are not good candidates for laser welding.
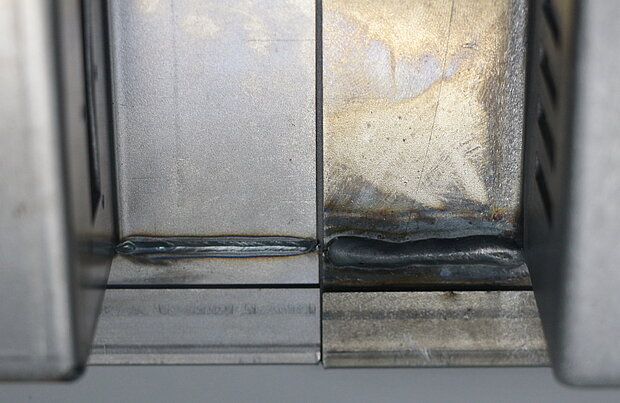
Laser Stir Welding - Laser Wobble Welding
Laser stir welding or Wobble Welding is a process in which a continuous beam laser is oscillated or wobbled at a relatively high frequency, which causes a stirring action within the molten weld pool – hence the term “stir welding or Wobble Welding.” The result is a manipulation of the weld pool/vapor cavity, which changes some key characteristics of the weld.
Benefits:
- Laser Stir Welding results in largely defect free joints, with no hot cracking, porosity or solidification cracks.
- More precise control of the weld pool for increased keyhole stability.
- Improved control of the profile and geometry of the weld – as an example, joints can be designed with more width at the root of the weld, which can be very useful for Lap/Thru-/Blind welds.
- Weld profiles can be manipulated into asymmetry, such as increasing the penetration on one side of the weld joint.
- Patterns can be programmed to compensate for large gaps in weld joints and other potentially problematic weld geometry problems.
- Higher feed rates can be achieved than with pulsed laser techniques.
- No filler materials is required.
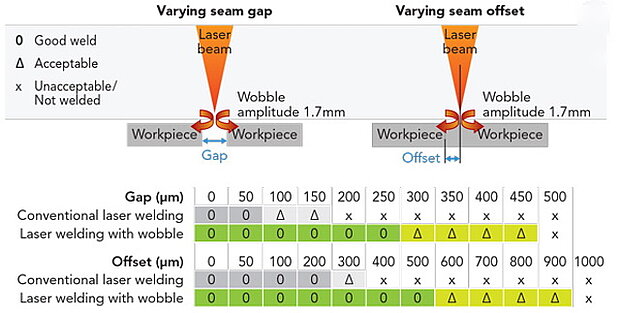
Due to the small spot size of the laser, the heat input is typically 200 times lower than with arc welding processes like MIG, MAG or TIG welding.
To fully reap the benefits of laser welding, a fabricator must commit with a normal laser welding machine to higher-quality sheet metal processing prior to welding.
As a rule of thumb: material gaps in the weld zone should be limited to approximately maximum 0.10~0.12mm, although this can limit can be extended to gaps of 0.50~0.80mm and more with our new photonweld laser welding torch with adjustable welding width.
Luckily, these tolerances are easily met by modern 2D laser cutting machines and press brakes. Although parts can typically be converted from arc welding to laser welding with just minor adjustments to the design, laser welding does provide design engineers with new opportunities, such as overlap welds, corner welds and flange welds. Even complex joint geometries like curved shapes or materials with different sheet thicknesses can be laser welded easily.
Reduced HAZ - Reduced Heat-Affected-Zone
Almost invisible Heat Affected zone
Most of a laser’s energy goes into making the weld itself, with very little wasted on heating the surrounding area. Less waste means lower utility bills.
Industrial Laser Welding Systems
Industrial laser welding has had a dramatic impact in the Machine Tool Industry over the years and has become the answer to many problems brought about by traditional welding methods. Many metalworking companies have turned to laser spot and laser seam welding due to these advantages. Automation, high welding speeds and contact-free processing help laser welding users achieve economic advantages very quickly.
Since laser welding produces pure, concentrated energy, it creates deeper welds while leaving high production output. This is one of the many reasons laser spot and seam welding systems are used in manufacturing in this industry. Items we use every day in our gadgets, electronics and parts have gone through laser welding technology in the course of their production.
Laser Spot Welding & Laser Seam Welding
Laser spot welding, laser seam welding, and direct welding are highly useful and slightly differing applications of laser welding technology. Laser spot and seam welding refer to welding functions applied to a single point or along a line. By setting a laser welding system to a high speed and extremely narrow weld geometry, the laser welder can produce extremely fine spot welding. Also, you can adjust the system to weld on continuous wave mode, welding with several kilowatts of power. The ideal laser speed for laser spot or seam welding projects varies according to the particular laser model, the laser power setting, and the material being laser welded.
Laser Welding Advantages in short
The use of lasers for welding has some distinct advantages over other welding techniques. Many of these advantages are related to the fact that with laser welding a 'keyhole' can be created. This keyhole allows heat input not just at the top surface, but through the thickness of the material(s). The main advantages of this are detailed below:
Speed and flexibility
Laser welding is a very fast technique. Depending on the type and power of laser used, thin section materials can be welded at speeds of many metres a minute. Lasers are, therefore, extremely suited to working in high productivity automated environments. For thicker sections, productivity gains can also be made as the laser keyhole welding process can complete a joint in a single pass which would otherwise require multiple passes with other techniques. Laser welding is nearly always carried out as an automated process, with the optical fibre delivered beams from laser diodes or fibre lasers in particular being easily remotely manipulated using multi-axis robotic delivery systems, resulting in a geometrically flexible manufacturing process.
Deep, narrow welds
Laser welding allows welds to be made with a high aspect ratio (large depth to narrow width). Laser welding, therefore, is feasible for joint configurations that are unsuitable for many other (conduction limited) welding techniques, such as stake welding through lap joints. This allows smaller flanges to be used compared with parts made using resistance spot welding.
Low distortion and low heat input
Lasers produce a highly concentrated heat source, capable of creating a keyhole. Consequently, laser welding melts only a very volume of weld metal, and transmits only a limited amount of heat into the surrounding material, and consequently all welded parts distort much less than those welded with many other processes. Another advantage resulting from this low heat input is the VERY narrow width of the heat affected zones either side of the weld, resulting in less thermal damage and loss of properties in the parent material adjacent to the weld.
Suitable for a wide range of materials and thicknesses
With lasers, many different materials can be welded or joined, both metallic and non-metallic, and including steels, stainless steels, Al, Ti and Ni alloys, plastics and textiles. Furthermore, taking the example of steels, the thickness of the material that can be welded can be anything from under a millimetre to around 30mm , depending on the type and power of laser used.
Performed out of vacuum
Unlike the majority of electron beam keyhole welding operations, laser welding is carried out at atmospheric pressure, although gas shielding is often necessary, to prevent oxidation of the welds.
Non-contact, single-sided process
Laser welding does not apply any force to the workpieces being joined, and more often or not is a single sided process, ie completing the joint from one side of the workpieces. However, in common with many other fusion processes, weld root shielding can be required from the opposite side.