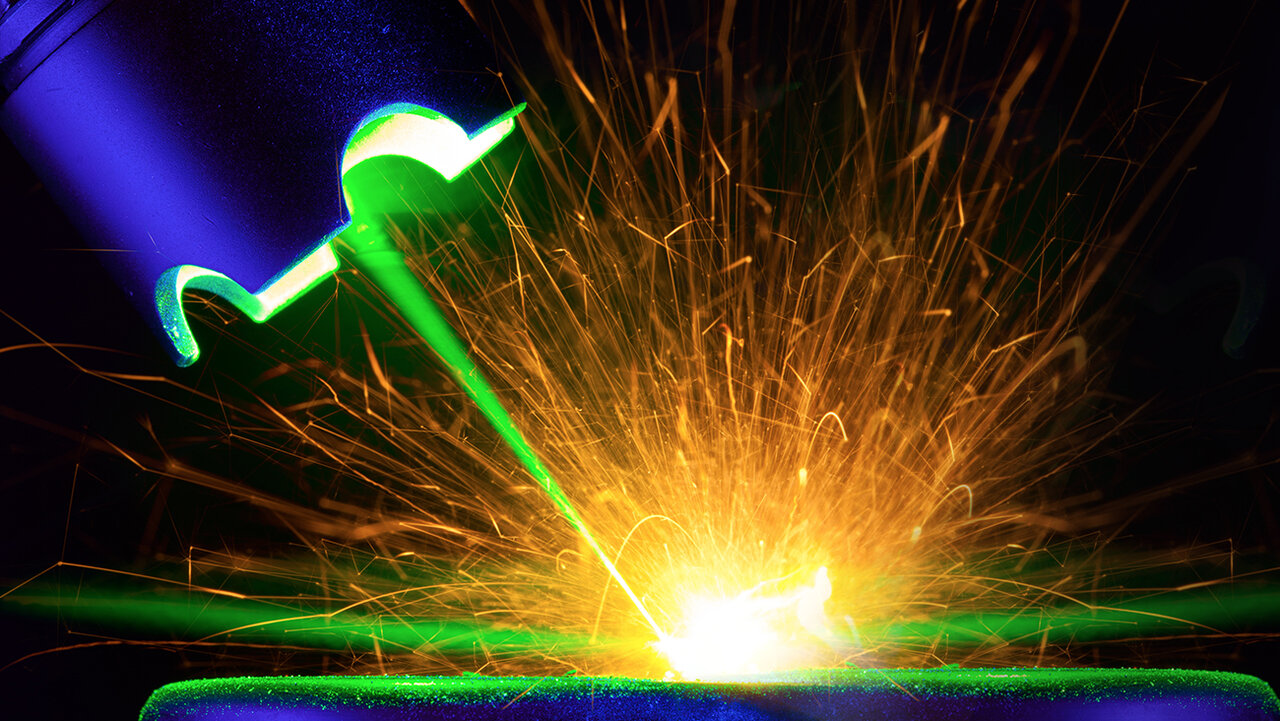
Shield Gas in Laser Welding
Selecting and Delivering Shield Gas in Laser Welding
In laser welding, shielding gas is a critical component used to protect the weld area from atmospheric contamination. The high-intensity laser beam used in this type of welding generates a significant amount of heat, creating a molten pool of metal. Without this shielding gas, the hot metal would be highly reactive to the oxygen, nitrogen, and hydrogen in the air, leading to a variety of weld defects, such as porosity, oxidation, or a weakened weld joint.
The shielding gas, often an inert gas or semi-inert gas, forms a protective barrier around the weld area, displacing the surrounding air and effectively “shielding” the weld pool from the atmosphere until the molten metal has solidified. This prevents oxidation from occurring and ensures that the molten metal remains clean and free from impurities.
In laser welding, the shielding gas, sometimes referred to as ‘cover gas’, has five main roles:
- Protect the weld metal from reacting with the ambient environment, (e.g. oxygen, nitrogen, hydrogen)
- Protective gas can protect the laser head lens from metal vapor pollution and liquid droplet sputtering.
- Prevent or minimize formation of a plasma, or cloud of ionized gas, that can form above the weld. The plasma is undesirable since it can partially block and/or distort the focused laser beam. The metal vapor absorbs the laser beam and ionizes into a plasma cloud. If there is too much plasma, the laser beam is consumed by the plasma to some extent. The shielding gas can disperse metal vapor plumes or plasma clouds, reduce the protective effect of the laser, and increase the effective utilization rate of the laser.
- Maintain a stable process and stable weld pool.
- Cool down the welding torch and keep the torch on a stable temperature
In general, the type of shielding gas used during high power laser welding process can play an important role in the process and can affect the resulting weld through influences on welding speed, microstructure, and shape.
The most frequently used shield gases for laser welding are helium, argon and nitrogen.
There are currently two main ways to blow-in protective gas:
- It is the side-blow protection of the side shaft
- It is coaxial protection (standard in our PhoyonWeld laser Welding Machines
Shield gas is typically directed centrally at the laser/material interface. A variety of methods, including coaxial nozzles, tubing, and the so-called ‘shoe’ may be used. The ‘shoe’ is particularly useful for metals, such as titanium, which must be shielded over a wider range of temperature as the weld cools.
The shielding gas blown in not only needs to protect the weld pool in a timely manner, but also needs to protect the just solidified area that has been welded. Therefore, side-shaft side blowing protection is generally used, because this method of protection is relatively The protection range of the coaxial protection method is wider, especially for the area where the weld has just solidified.
Sideshaft side blowing For engineering applications, not all products can be protected by sideshaft side blowing. For some specific products, only coaxial protection can be used. It needs to be targeted from the product structure and joint form.
For whichever shielding gas type and delivery method used, too low gas flow will result in a heavy oxidized weld surface while too high gas flow causes excessive weld undercut and a disrupted weld bead. Shield gas delivered using an auxiliary tube design is typically aimed at the trailing portion of the weld (hot material).
In most cases, underbead (bottom surface) shielding is not required for welding at speeds greater than 1m/min. However, for stainless steels, nickel alloys, titanium alloys and aluminum alloys, underbead shielding is recommended to produce an acceptable appearance of the weld. For full penetration welds requiring protection of the bottom side of the weld, fixturing is often designed to incorporate a means of delivering the shield gas to the bottom side.
The table below provides a comparison of these and other shield gases used for laser welding
Shield Gas | Plasma suppression | Prevention against oxidation | Relative cost | Typical flow rates | Weld profile | Limitations |
---|---|---|---|---|---|---|
He | Excellent | Good | High | 20-40l/min | Deepest penetration | None |
Ar | Lower | Excellent | Medium | 12-25l/min | Wide | Plasma cloud reduces power density |
N2 (O2 free) | Lower | Good | Low | 15-25l/min | Deepest penetration | Embrittlement of certain alloys (ex Ti) |
CO2 | Lower | Poor | Lowest | 20-45l/min | Nominal | No usefull for reactive materials |
He+Ar (20/80%) | Good | Very Good | Medium | 20-35l/min | Nominal | None |
Effects of The Shielding Gas
The shielding gas plays a very important role in the welding process. Let’s take a look at its impact on the laser welding process.
Positive Effects
The choice of shielding gas in laser welding plays a crucial role in determining the quality and properties of the weld. Different types of shielding gases can have various positive effects on the welding process.
- Penetration depth and bead shape: The composition of the shielding gas can influence how deeply the laser beam penetrates into the material and how the molten metal forms during solidification. By selecting an appropriate shielding gas, welders can achieve optimal results with laser welding machines and laser welding equipment, ensuring the desired penetration depth and bead shape for sheet metal.
- Protect the weld pool from atmospheric contamination: When a laser beam interacts with the material, it generates high temperatures that can cause oxidation or other reactions with elements present in the air. Shielding gases act as a barrier, preventing these unwanted interactions and ensuring a clean environment for welding.
- Reducing spatter: The ionization energy of different gases also affects their effectiveness as shielding agents. Gases with low ionization energy are more likely to ionize and form plasma when exposed to high-energy laser beams. This plasma helps maintain a stable arc during welding, improving control over heat input and reducing spatter.
Negative Effects
While there are numerous advantages to using shielding gases in laser welding, it’s essential to consider potential negative effects as well.
- Improper use of the protective gas may cause deformation. Excessive reliance on shielding gases may lead to surface defects if not used correctly or if inadequate protection is provided during welding. Welders need to carefully balance factors such as gas flow rate, nozzle design, and distance between the nozzle tip and workpiece surface to ensure proper coverage without causing issues like porosity or lack of fusion.
- Choosing the wrong type of blow can have adverse effects. It’s worth noting that different materials may react differently to specific types of shielding gases. For example, certain gases may be more suitable for welding stainless steel, while others are better suited for welding aluminum alloys or carbon steel. Welders must consider the material being welded and select a shielding gas that complements its properties to achieve optimal results with laser welding equipment.
The role of shielding gas in laser welding
What shielding gas should I use for laser welding?
In laser welding, shielding gas will affect not only the weld formation, the weld quality, the weld depth, and the weld width, etc. In most cases, the blowing of the shielding gas will have a beneficial effect on the weld, but bad use may also bring adverse effects.
The positive effect of shielding gas on laser welding
- Proper blowing of the shielding gas will effectively protect the weld pool from oxidation and even avoid oxidation;
- Proper blowing of the shielding gas can effectively reduce the splash generated during the welding process and protect the focusing mirror;
- Proper blowing of the shielding gas can promote the uniform spreading of the weld pool during solidification so that the weld is uniformly formed and beautiful;
- Proper blowing of the shielding gas can effectively reduce metal vapor or the shielding effect of the plasma cloud on the laser so that the laser energy reaching the surface of the workpiece, and thereby increase the effective utilization rate of the laser;
- Proper blowing of the shielding gas can effectively reduce weld porosity.
As long as the gas type, gas flow rate, and blowing method are correctly selected, the ideal effect can be obtained. However, improper use of shielding gas can also have adverse effects on welding.
Adverse effects of improper use of shielding gas on laser welding
- Improper blowing of shielding gas may cause the weld to deteriorate;
- Choosing the wrong type of gas may cause cracks in the weld, and may also lead to the reduction of weld mechanical properties;
- Choosing the wrong type of gas may cause the weld to be more oxidized (whether the flow is too large or too small), or it may cause the weld pool metal to be seriously disturbed by the external force to cause the weld to collapse or form unevenly;
- Choosing the wrong gas blowing method will result in the weld not achieving the protective effect or negatively affecting the weld formation;
- Insufflation of the shielding gas will have a certain effect on the weld penetration, especially when the thin plate is welded, the weld penetration will be reduced.
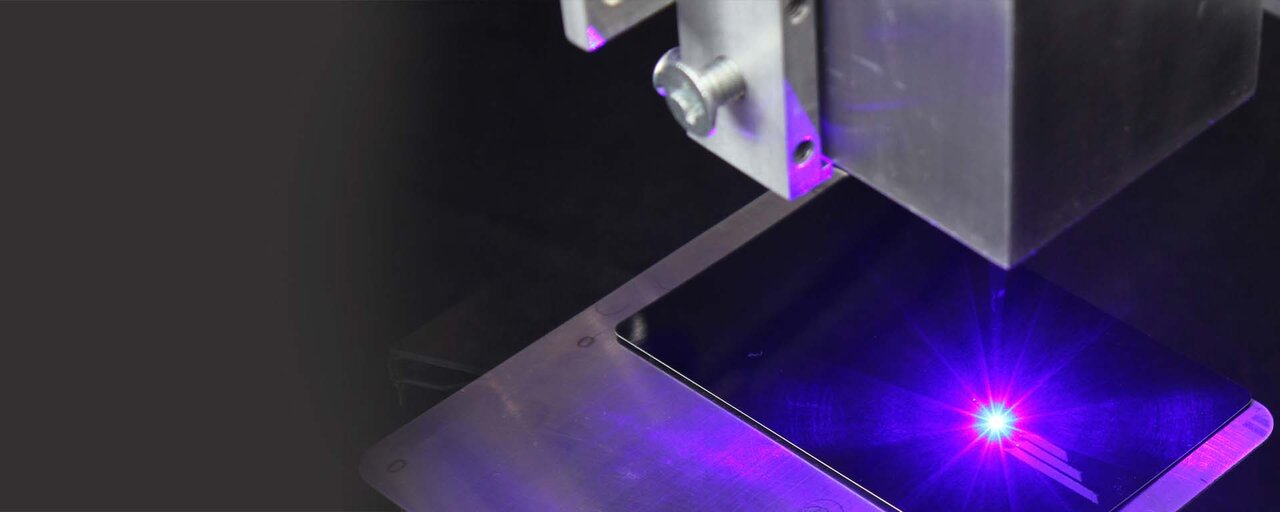
Shield gas reaction with weld metal
Which gas does react with metals during laser welding?
Certain metals and alloys react with nitrogen in a way that changes the microstructure of the weld. For example, nitrogen reacts strongly with titanium to form titanium-nitride compounds that can make the laser weld brittle. For this reason, argon is the preferred shield gas for welding titanium-based alloys.
This is also the case for certain types of stainless steels. Nitrogen should not be used for welding austenitic stainless steels alloyed with titanium and niobium. Nitrogen forms nitrides with these elements, reducing the amount of free titanium and niobium available for preventing chromium carbide formation and sensitivity to intergranular corrosion.
For ferritic stainless steel, nitrogen shield gas has the same effect as carbon. Introduction of nitrogen into the material during welding of ferritic steels leads to an increased quantity of martensite in the weld metal. This, in turn, can make the weld more brittle and more susceptible to hydrogen embrittlement.
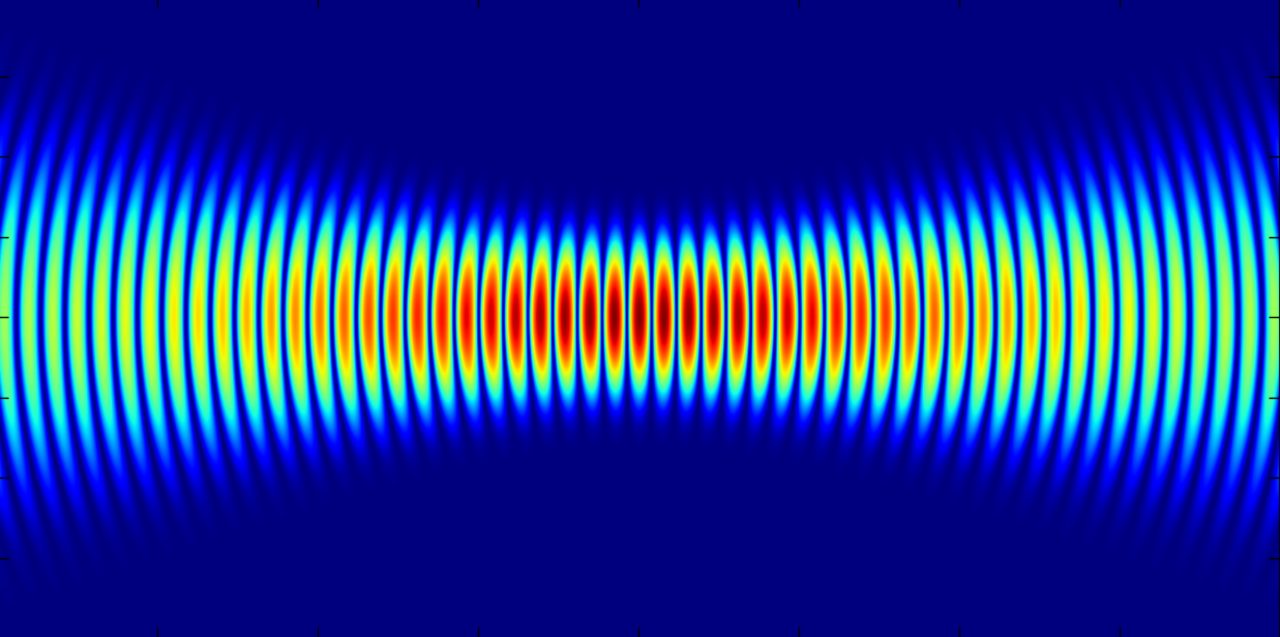
ARGON GAS FOR LASER WELDING
Lasermach Does recommend Argon gas for its laser welding machines
WHAT IS ARGON GAS?
Argon gas is a chemical element with Symbol Ar, and one of the noble gases. Argon is also the 3rd most abundant gas on earth. Argon is most commonly used as an inert shielding gas. Argon is Colorless, odorless, Non-Flammable, and Non-Toxic.
WHY DO LASER WELDING SYSTEMS USE ARGON?
Argon is used as a preferred shielding gas in Laser Welding Systems. During the welding, process metals are exposed to temperatures of upwards of 7000 Degrees. At these temperatures, all metals become liquid, which allows the formation of the weld. Argon is used to protect the molten pool of metal against elements in the Atmosphere including Oxygen, Nitrogen, and Hydrogen. These elements cause reactions with the molten liquid weld pool, such as porosity and increased weld spatter. Argon also plays an important role to have increased weld penetration, better filler wire transfer, and better weld appearance.
IS ARGON DANGEROUS?
Argon has safety concerns to be aware of, but for the most part is a very safe gas. It is non-toxic and non-flammable, therefore it is not poisonous, and it will not burn. Argon does come in a compressed tank, and proper safety protocol should be followed when working with compressed tanks. Argon is 38% denser than air so when working within confined areas ensure that you have proper air ventilation. The amount of Argon used in the laser welding is relative small and is of very little safety concern.
WHAT KIND OF ARGON GAS DO I GET?
We recommend using 99.996% pure Argon (Argon 4.6). This is one of the most commonly used welding gasses in the world. Every major gas supply company will carry this. It is the same as welding gas used in a traditional TIG welding Setup. Pure Argon refers to the gas being just Argon, and not mixed with another gas. Other shielding gasses such as CO2 and Argon CO2 mixes, do not work as well as pure argon.
Ultra high purity or medical grade Argon is not required.