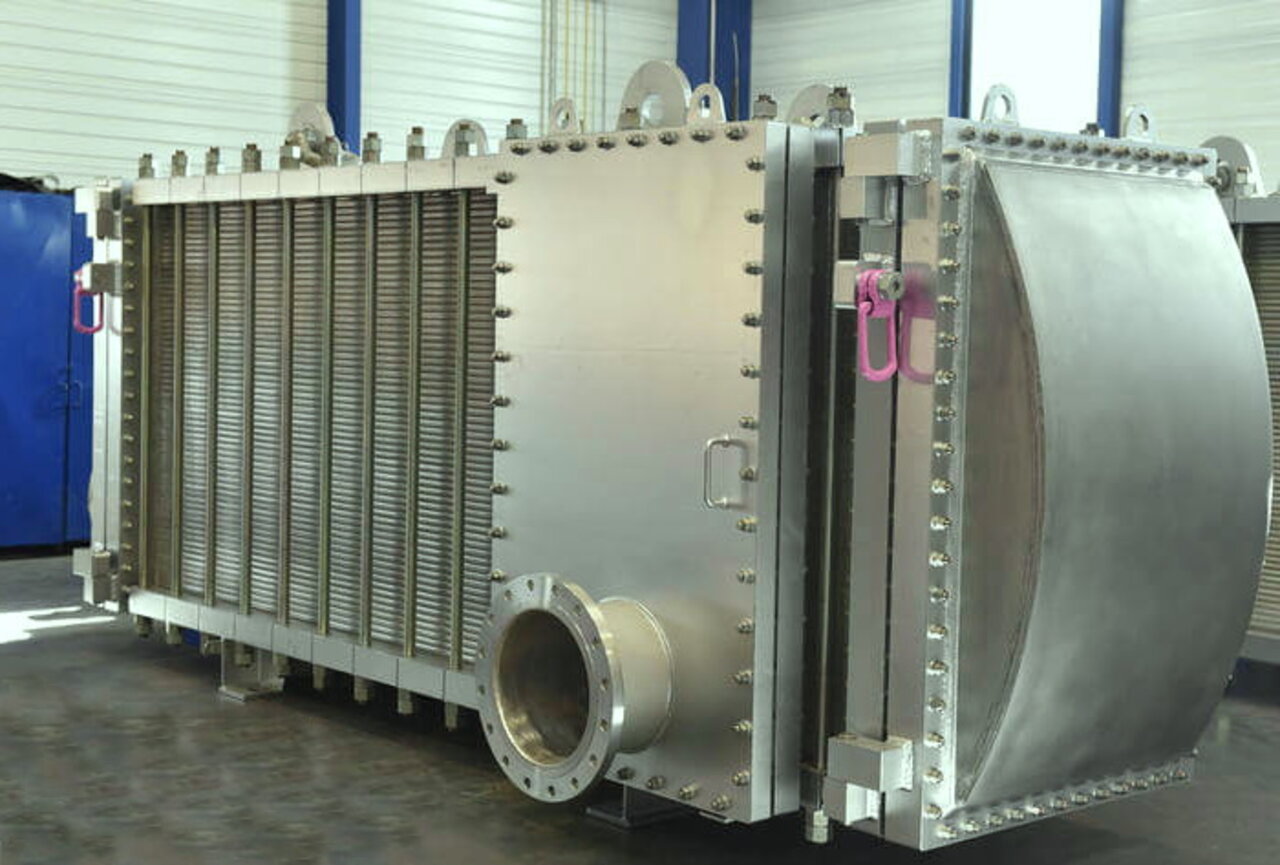
In the heat transfer market, most experts are familiar with plate heat exchangers or PHE's. Initially introduced for hygiene purposes for the dairy industry and subsequently developed in a variety of uses, they consist of several parallel plates. The plates are corrugated to increase turbulence, exchange surface and give them a certain mechanical rigidity. In addition PHEs have flow passages for flow of fluids at the corners, and the plates have gaskets to control flow and prevent leakage. The corrugated plates are combined to create complex channels through which a hot and cold fluid are distributed. The two fluids flow inside the exchanger in the passages between the plates; this without mixing on either side of the corrugated plate. Energy is thus transferred from one to the other as they flow side by side without touching each other.
There is a special type of plate heat exchanger for the condensation of halogenated refrigerant fluids called “brazed plate heat exchanger”. The brazed plate heat exchanger has the characteristic of being a stainless steel plate heat exchanger where the gaskets are absent. It is assembled using a special vacuum furnace brazing technology, which makes it possible to create a very compact, durable and highly reliable unit. Brazing spots hold the various plates together, and the heat exchanger is tightly fixed. Now with our Wobble technology we can replace all complex and expensive brazing by simple laser welding, which goes much faster, cost much less and is more rigid.
In fact, while the various Brazed PHE plates are still slightly movable and not so resistant, the Wobble+ laser welded PHE's have strongly welded plates together, eliminating any mobility, which makes it more efficient, reliable and economical, reducing costs in the long run. The Brazed plate Heat Exchanger is mostly made of copper or nickel: in this case, with these materials, the heat exchanger will work with all refrigerants except ammonia. For ammonia, we will have BPHEs with stronger metal alloys like stainless and laser welded channels alternating with those with a gasket. The refrigerant flows through the welded channels, and is in contact with the gaskets in the circular holes.
What is a heat exchanger?
A heat exchanger is a device used to transfer heat between a solid object and a fluid, or between two or more fluids. The fluids may be separated by a solid wall to prevent mixing or they may be in direct contact. They are widely used in space heating, refrigeration, air conditioning, power stations, chemical plants, petrochemical plants, petroleum refineries, natural-gas processing, and sewage treatment. The classic example of a heat exchanger is found in an internal combustion engine in which a circulating fluid known as engine coolant flows through radiator coils and air flows past the coils, which cools the coolant and heats the incoming air. Another example is the heat sink, which is a passive heat exchanger that transfers the heat generated by an electronic or a mechanical device to a fluid medium, often air or a liquid coolant.
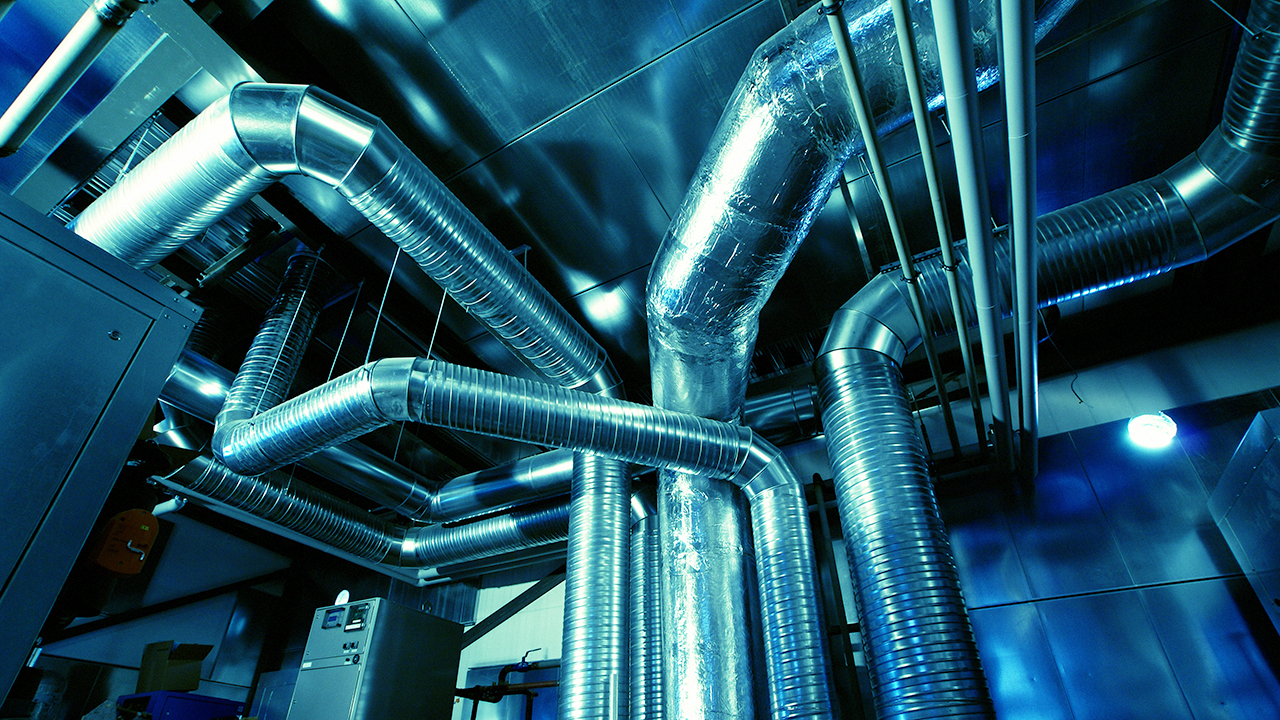
Types of heat exchangers
Double pipe heat exchangers are the simplest exchangers used in industries. On one hand, these heat exchangers are cheap for both design and maintenance, making them a good choice for small industries. On the other hand, their low efficiency coupled with the high space occupied in large scales, has led modern industries to use more efficient heat exchangers like shell and tube or plate. However, since double pipe heat exchangers are simple, they are used to teach heat exchanger design basics to students as the fundamental rules for all heat exchangers are the same.
Plate heat exchangers
Another type of heat exchanger is the plate heat exchanger. These exchangers are composed of many thin, slightly separated plates that have very large surface areas and small fluid flow passages for heat transfer. Advances in gasket and brazing technology have made the plate-type heat exchanger increasingly practical. In HVAC applications, large heat exchangers of this type are called plate-and-frame; when used in open loops, these heat exchangers are normally of the gasket type to allow periodic disassembly, cleaning, and inspection. There are many types of permanently bonded plate heat exchangers, such as dip-brazed, vacuum-brazed, and welded plate varieties, and they are often specified for closed-loop applications such as refrigeration. Plate heat exchangers also differ in the types of plates that are used, and in the configurations of those plates. Some plates may be stamped with "chevron", dimpled, or other patterns, where others may have machined fins and/or grooves. When compared to shell and tube exchangers, the stacked-plate arrangement typically has lower volume and cost. Another difference between the two is that plate exchangers typically serve low to medium pressure fluids, compared to medium and high pressures of shell and tube. A third and important difference is that plate exchangers employ more countercurrent flow rather than cross current flow, which allows lower approach temperature differences, high temperature changes, and increased efficiencies.
Plate and shell heat exchanger
A third type of heat exchanger is a plate and shell heat exchanger, which combines plate heat exchanger with shell and tube heat exchanger technologies. The heart of the heat exchanger contains a fully welded circular plate pack made by pressing and cutting round plates and welding them together. Nozzles carry flow in and out of the platepack (the 'Plate side' flowpath). The fully welded platepack is assembled into an outer shell that creates a second flowpath ( the 'Shell side'). Plate and shell technology offers high heat transfer, high pressure, high operating temperature, uling and close approach temperature. In particular, it does completely without gaskets, which provides security against leakage at high pressures and temperatures.
Plate fin heat exchanger
This type of heat exchanger uses "sandwiched" passages containing fins to increase the effectiveness of the unit. The designs include crossflow and counterflow coupled with various fin configurations such as straight fins, offset fins and wavy fins.
Plate and fin heat exchangers are usually made of aluminum alloys, which provide high heat transfer efficiency. The material enables the system to operate at a lower temperature difference and reduce the weight of the equipment. Plate and fin heat exchangers are mostly used for low temperature services such as natural gas, helium and oxygen liquefaction plants, air separation plants and transport industries such as motor and aircraft engines.
Advantages of plate and fin heat exchangers:
- High heat transfer efficiency especially in gas treatment
- Larger heat transfer area
- Approximately 5 times lighter in weight than that of shell and tube heat exchanger.
- Able to withstand high pressure
Disadvantages of plate and fin heat exchangers:
- Might cause clogging as the pathways are very narrow
- Difficult to clean the pathways
- Aluminum alloys are susceptible to Mercury Liquid Embrittlement Failure
Pillow plate heat exchanger
A pillow plate exchanger is commonly used in the dairy industry for cooling milk in large direct-expansion stainless steel bulk tanks. The pillow plate allows for cooling across nearly the entire surface area of the tank, without gaps that would occur between pipes welded to the exterior of the tank.
The pillow plate is constructed using a thin sheet of metal spot-welded to the surface of another thicker sheet of metal. The thin plate is welded in a regular pattern of dots or with a serpentine pattern of weld lines. After welding the enclosed space is pressurised with sufficient force to cause the thin metal to bulge out around the welds, providing a space for heat exchanger liquids to flow, and creating a characteristic appearance of a swelled pillow formed out of metal.
Shell and tube heat exchanger
Shell and tube heat exchangers consist of series of tubes. One set of these tubes contains the fluid that must be either heated or cooled. The second fluid runs over the tubes that are being heated or cooled so that it can either provide the heat or absorb the heat required. A set of tubes is called the tube bundle and can be made up of several types of tubes: plain, longitudinally finned, etc. Shell and tube heat exchangers are typically used for high-pressure applications (with pressures greater than 30 bar and temperatures greater than 260 °C). This is because the shell and tube heat exchangers are robust due to their shape.
Several thermal design features must be considered when designing the tubes in the shell and tube heat exchangers: There can be many variations on the shell and tube design. Typically, the ends of each tube are connected to plenums (sometimes called water boxes) through holes in tubesheets. The tubes may be straight or bent in the shape of a U, called U-tubes.
- Tube diameter: Using a small tube diameter makes the heat exchanger both economical and compact. However, it is more likely for the heat exchanger to foul up faster and the small size makes mechanical cleaning of the fouling difficult. To prevail over the fouling and cleaning problems, larger tube diameters can be used. Thus to determine the tube diameter, the available space, cost and fouling nature of the fluids must be considered.
- Tube thickness: The thickness of the wall of the tubes is usually determined to ensure:
- There is enough room for corrosion
- That flow-induced vibration has resistance
- Axial strength
- Availability of spare parts
- Hoop strength (to withstand internal tube pressure)
- Buckling strength (to withstand overpressure in the shell)
- Tube length: heat exchangers are usually cheaper when they have a smaller shell diameter and a long tube length. Thus, typically there is an aim to make the heat exchanger as long as physically possible whilst not exceeding production capabilities. However, there are many limitations for this, including space available at the installation site and the need to ensure tubes are available in lengths that are twice the required length (so they can be withdrawn and replaced). Also, long, thin tubes are difficult to take out and replace.
- Tube pitch: when designing the tubes, it is practical to ensure that the tube pitch (i.e., the centre-centre distance of adjoining tubes) is not less than 1.25 times the tubes' outside diameter. A larger tube pitch leads to a larger overall shell diameter, which leads to a more expensive heat exchanger.
- Tube corrugation: this type of tubes, mainly used for the inner tubes, increases the turbulence of the fluids and the effect is very important in the heat transfer giving a better performance.
- Tube Layout: refers to how tubes are positioned within the shell. There are four main types of tube layout, which are, triangular (30°), rotated triangular (60°), square (90°) and rotated square (45°). The triangular patterns are employed to give greater heat transfer as they force the fluid to flow in a more turbulent fashion around the piping. Square patterns are employed where high fouling is experienced and cleaning is more regular.
- Baffle Design: baffles are used in shell and tube heat exchangers to direct fluid across the tube bundle. They run perpendicularly to the shell and hold the bundle, preventing the tubes from sagging over a long length. They can also prevent the tubes from vibrating. The most common type of baffle is the segmental baffle. The semicircular segmental baffles are oriented at 180 degrees to the adjacent baffles forcing the fluid to flow upward and downwards between the tube bundle. Baffle spacing is of large thermodynamic concern when designing shell and tube heat exchangers. Baffles must be spaced with consideration for the conversion of pressure drop and heat transfer. For thermo economic optimization it is suggested that the baffles be spaced no closer than 20% of the shell’s inner diameter. Having baffles spaced too closely causes a greater pressure drop because of flow redirection. Consequently, having the baffles spaced too far apart means that there may be cooler spots in the corners between baffles. It is also important to ensure the baffles are spaced close enough that the tubes do not sag. The other main type of baffle is the disc and doughnut baffle, which consists of two concentric baffles. An outer, wider baffle looks like a doughnut, whilst the inner baffle is shaped like a disk. This type of baffle forces the fluid to pass around each side of the disk then through the doughnut baffle generating a different type of fluid flow.
Fixed tube liquid-cooled heat exchangers especially suitable for marine and harsh applications can be assembled with brass shells, copper tubes, brass baffles, and forged brass integral end hubs.
Adiabatic wheel heat exchanger
A fourth type of heat exchanger uses an intermediate fluid or solid store to hold heat, which is then moved to the other side of the heat exchanger to be released. Two examples of this are adiabatic wheels, which consist of a large wheel with fine threads rotating through the hot and cold fluids, and fluid heat exchangers.
Fluid heat exchangers
This is a heat exchanger with a gas passing upwards through a shower of fluid (often water), and the fluid is then taken elsewhere before being cooled. This is commonly used for cooling gases whilst also removing certain impurities, thus solving two problems at once. It is widely used in espresso machines as an energy-saving method of cooling super-heated water to use in the extraction of espresso.
Dynamic scraped surface heat exchanger
Another type of heat exchanger is called "(dynamic) scraped surface heat exchanger". This is mainly used for heating or cooling with high-viscosity products, crystallization processes, evaporation and high-fouling applications. Long running times are achieved due to the continuous scraping of the surface, thus avoiding fouling and achieving a sustainable heat transfer rate during the process.
Phase-change heat exchangers
In addition to heating up or cooling down fluids in just a single phase, heat exchangers can be used either to heat a liquid to evaporate (or boil) it or used as condensers to cool a vapor and condense it to a liquid. In chemical plants and refineries, reboilers used to heat incoming feed for distillation towers are often heat exchangers. Distillation set-ups typically use condensers to condense distillate vapors back into liquid.
Power plants that use steam-driven turbines commonly use heat exchangers to boil water into steam. Heat exchangers or similar units for producing steam from water are often called boilers or steam generators. In the nuclear power plants called pressurized water reactors, special large heat exchangers pass heat from the primary (reactor plant) system to the secondary (steam plant) system, producing steam from water in the process. These are called steam generators. All fossil-fueled and nuclear power plants using steam-driven turbines have surface condensers to convert the exhaust steam from the turbines into condensate (water) for re-use.
To conserve energy and cooling capacity in chemical and other plants, regenerative heat exchangers can transfer heat from a stream that must be cooled to another stream that must be heated, such as distillate cooling and reboiler feed pre-heating. This term can also refer to heat exchangers that contain a material within their structure that has a change of phase. This is usually a solid to liquid phase due to the small volume difference between these states. This change of phase effectively acts as a buffer because it occurs at a constant temperature but still allows for the heat exchanger to accept additional heat. One example where this has been investigated is for use in high power aircraft electronics.
Heat exchangers functioning in multiphase flow regimes may be subject to the Ledinegg instability.
Direct contact heat exchangers
Direct contact heat exchangers involve heat transfer between hot and cold streams of two phases in the absence of a separating wall. Thus such heat exchangers can be classified as:
- Gas – liquid
- Immiscible liquid – liquid
- Solid-liquid or solid – gas
Most direct contact heat exchangers fall under the Gas – Liquid category, where heat is transferred between a gas and liquid in the form of drops, films or sprays. Such types of heat exchangers are used predominantly in air conditioning, humidification, industrial hot water heating, water cooling and condensing plants.
Microchannel heat exchangers
Micro heat exchangers, Micro-scale heat exchangers, or microstructured heat exchangers are heat exchangers in which (at least one) fluid flows in lateral confinements with typical dimensions below 1 mm. The most typical such confinement are microchannels, which are channels with a hydraulic diameter below 1 mm. Microchannel heat exchangers can be made from metal, ceramic. Microchannel heat exchangers can be used for many applications including:
- high-performance aircraft gas turbine engines
- heat pumps
- air conditioning
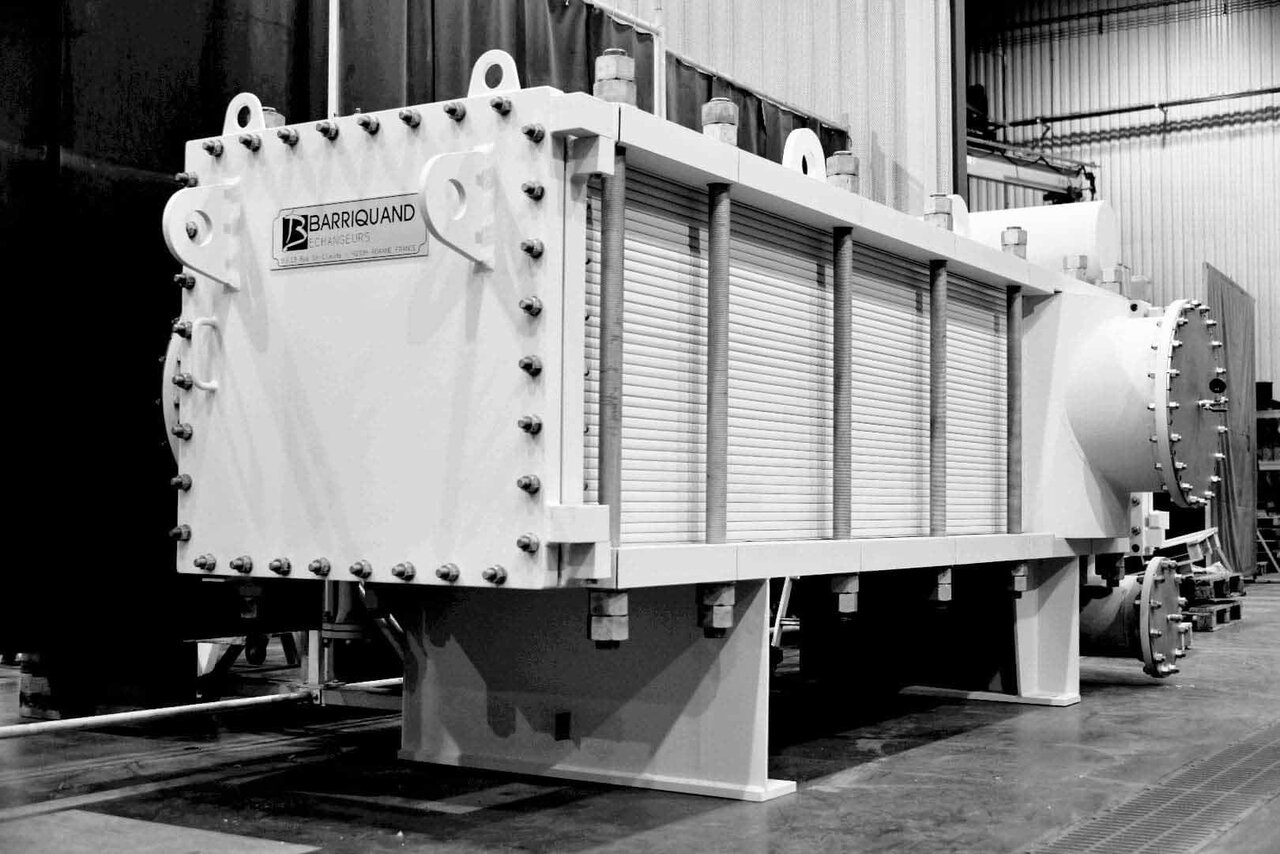
Plate heat exchangers, often called plate-and-frame heat exchanger, have a major advantage over (high heat transfer rate) other types of heat exchangers in that the fluids are exposed to a much larger surface area.
The plate heat exchanger consists of a frame with end plates which squeeze the corrugated heat transfer plates. Within plate heat exchangers, the fluid paths alternate between plates allowing the two fluids to interact(heat or cool one fluid by transferring heat between it and another fluid, but not mix).
- Plate Heat Exchangers have various applications-
- petrochemical
- pharmaceutical
- power
- industrial dairy
- chemical
- food and beverage industry
Types of Plate Heat Exchangers
There are four main types of plate heat exchanger
- Brazed Plate Heat Exchanger
- Gasketed Plate Heat Exchanger
- Welded Plate Heat Exchanger
- Semi-Welded Plate Heat Exchanger
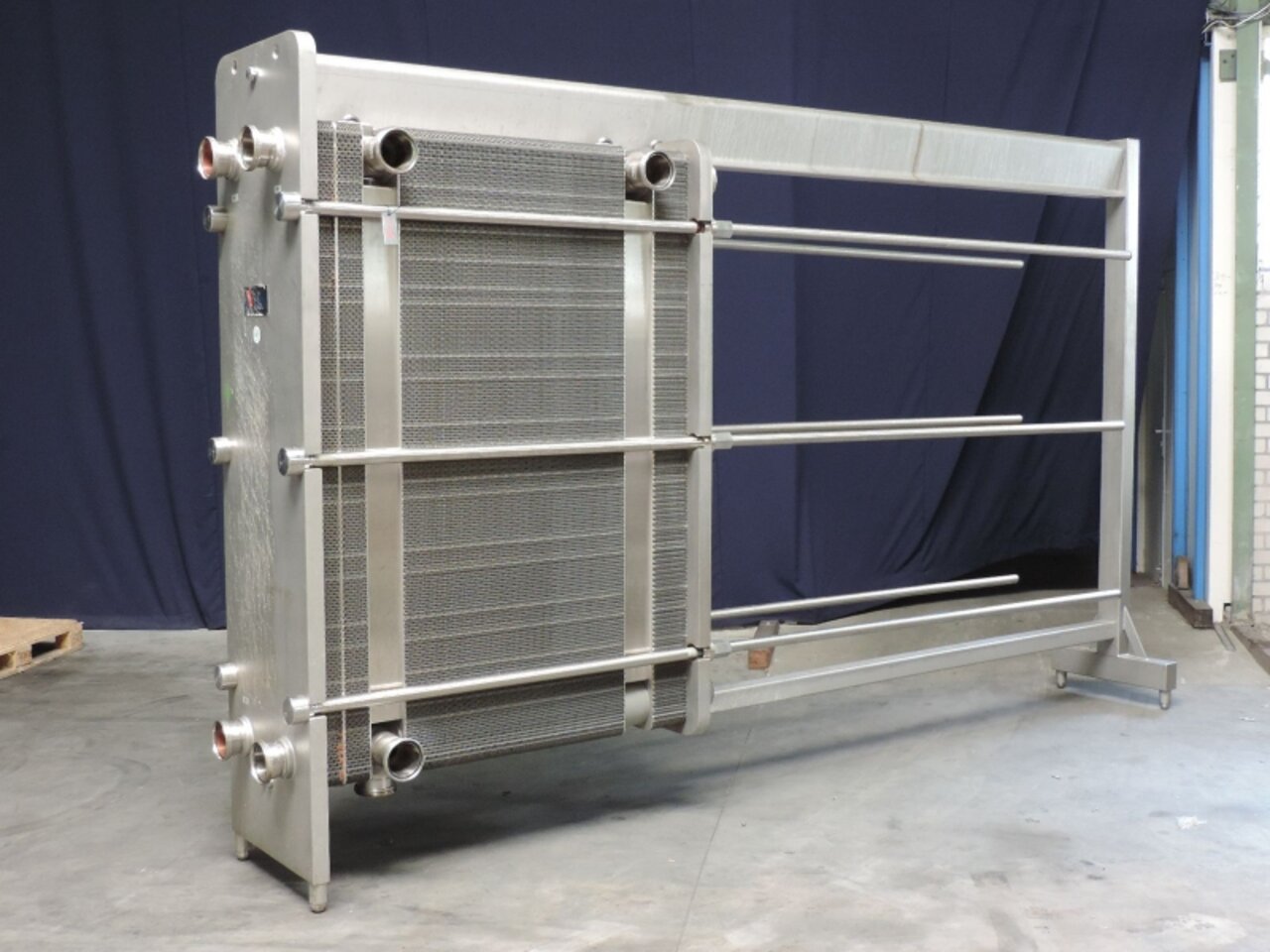
Gasketed Plate Heat Exchangers
High quality gaskets are designed to protect against leaks and seal plates together. Plates can easily be removed for expansion, cleaning, or replacing purposes. These design can drastically reduce the costs of maintenance.
- Typical applications of Gasketed Plate Heat Exchanger
- Oil cooling
- Heat transfer fluids
- Hazardous liquids
- Process chemicals
Semi-Welded Plate Heat Exchangers
A mixture of welded and gasketed plates. This type of heat exchanger contain pairs of two plates welded together which are gasketed to other pairs, therefore one fluid path is welded and the other fluid path is gasketed. It's easy to service on one side and able to transfer more intense fluids on the other. Semi-Welded heat exchanger type is perfect choice for transferring expensive materials because it has a very low risk of fluid loss.
- Typical applications of Semi-Welded Plate Heat Exchanger
- Heat transfer fluids
- Oil cooling
- Process chemicals
- Hazardous liquids
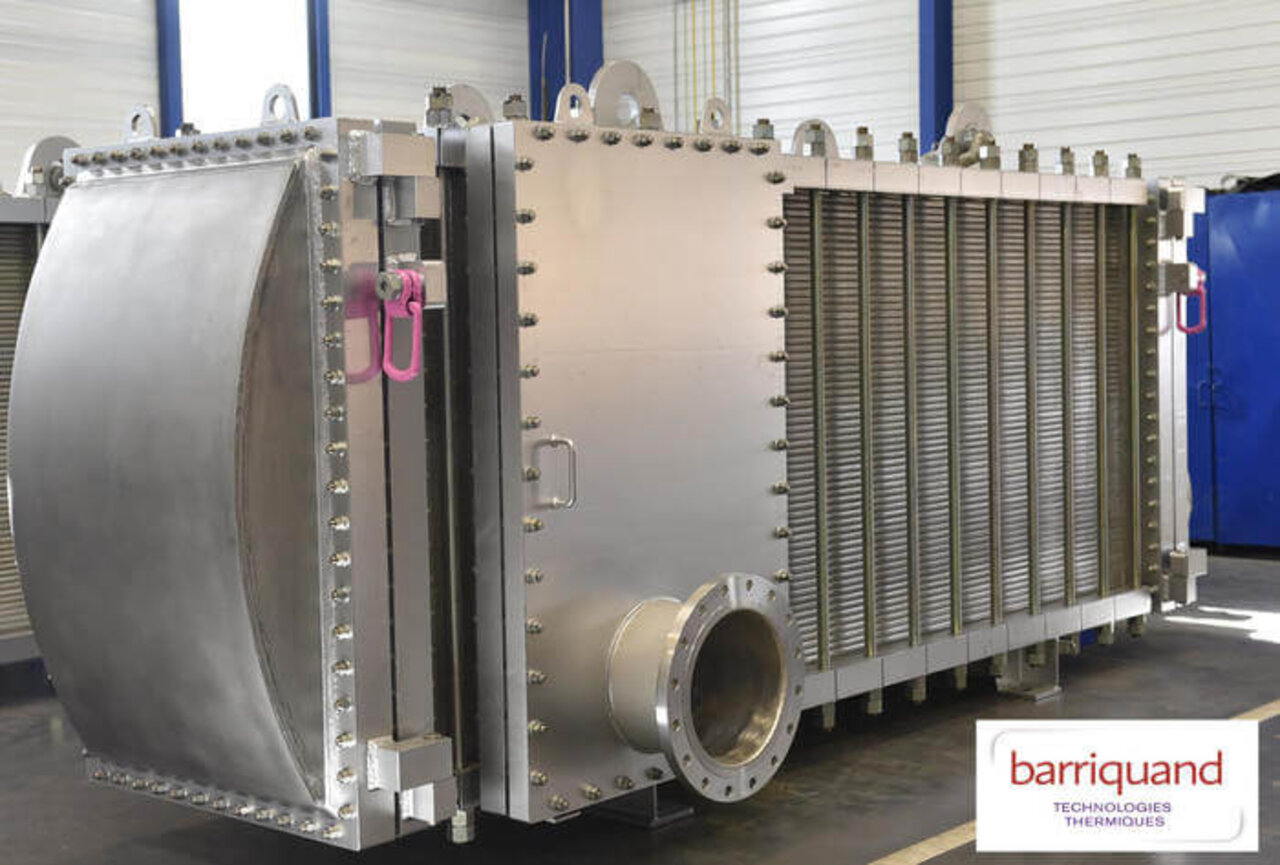
Heat exchangers all work by passing a hot fluid and a cold fluid across opposite sides of a piece of metal. The heat from one fluid passes across the metal (which is thermally conductive) into the other fluid without the fluids making contact. High fluid velocity, high turbulence, high surface area and a large temperature differential all contribute to more efficient heat transfer. However, different designs are more efficient than others depending on the application.
There are three common kinds of heat exchangers. They can all be effective in a variety of heat transfer applications, but optimizing efficiency, cost and space depends heavily on the particular process in which the heat exchanger is installed. This article explains the basic qualitative differences between common heat exchangers to help you decide which is most appropriate for your application.
Shell and Tube Heat Exchangers
Shell and tube heat exchangers are aptly named – the primary components are a tube pack (above, right) and a shell to contain them. One fluid goes through the tubes, and the second goes through the larger shell, surrounding the tubes. The prototypical shell and tube heat exchanger has only one inner tube, and is typically used to teach engineering students the basic concept of a heat exchanger. However, in practice, a pack of smaller tubes is much more effective because it greatly increases the heat transfer surface area (and has a minor positive effect on turbulence to boot).
The shell and tube heat exchanger in the photo above has about twelve times the efficiency than a hypothetical single-tube heat exchanger of the same size. However, there is a disadvantage to smaller tubes – if the fluid in your application is very viscous or has particulates, it can foul up the tube and undermine the heat transfer process.
Shell and tube heat exchangers dominated the heat exchanger market up until the latter part of the 20th century, as plate heat exchangers began to replace them in many industrial and most HVAC applications.
Due to their simple design, they also hold a prominent place in engineering curricula around the globe. They have many advantages that helped them earn those achievements. First, they’re relatively cheap – they’re essentially just a bunch of tubes. Also, due to their hydro- and aerodynamic design, they can support higher operating temperatures and pressures than your typical plate heat exchanger, which, due to its compactness, has to change the direction of flow many times per cycle. This also means that the pressure drop from input to output is smaller, which can save on energy costs.
Despite the advantages, plate heat exchangers are becoming preferred due to better heat transfer (we’ll see why in a moment), easier maintenance and cleaning, modularity and compactness.
Plate and Frame Heat Exchanger (Plate Heat Exchangers)
Plate heat exchangers are constructed with a series of plates held together in a large frame. There are two inputs and two outputs, and the spaces between plates alternate between the two liquids (hot, cold, hot, cold, etc. as shown above, right). This design lends itself to very high heat transfer efficiency due to large surface area – much higher than a shell and tube heat exchanger taking up similar space. Plate heat exchangers are also much easier to clean and maintain, because they’re designed to be relatively easy to disassemble and inspect. Also, if there is a defect in a plate, you can simply remove two plates and put the unit right back in service at slightly lower capacity while you wait for replacements. Shell and tube heat exchangers do not share this luxury.
While all plate heat exchangers have corrugated plates, they can differ by how they seal the plates together. In ascending order of leak resistance (and price), plate heat exchangers can be gasketed, brazed or welded. Gaskets, while more susceptible to failure under pressure, are inexpensive and easy to replace. They also offer the indispensable benefit of modularity – a gasketed plate heat exchanger can be completely disassembled, and plates can be added to increase capacity at any time. If a plate heat exchanger is brazed or welded, it’s very difficult and expensive to add plates after the fact. In general, gasketed plate heat exchangers are preferred in industrial settings where flexibility is paramount. Welded plate heat exchangers are rare due to the increased cost, but brazed plate heat exchangers are common in HVAC settings where replacement is easier than maintenance.
Dimple Plate/Plate Coil Heat Exchanger
Although its market share is much less than that of the previous two categories, dimple plate/plate coil technology is the best solution for applications where one of the fluids isn’t moving. It’s also useful in retrofit applications, such as waste heat recovery that wasn’t accounted for in the initial blueprints. In general, this is a good option for passive heating or cooling a storage tank (such as a bright beer tank or dairy tank) where refrigeration or heating would otherwise be expensive.
The premise is very simple – two steel sheets are spot-welded together, then inflated to make channels between the plates for fluid to flow. Due to its simplicity and low-cost materials, dimple plate/plate coil technology can generally be customized to any particular application. The most prevalent application is tank jackets for beer and dairy tanks, but sections of dimple plate can also be cut to fit inside a tank and submerged in the stored liquid for efficient heat transfer.
Dimple plate/plate coil offers the best of both above kinds of heat exchangers – it’s cheap, customizable and compact, but can withstand incredibly high pressures and temperatures due to design and materials. It can also be added as an afterthought to many industrial processes, most notably to cut energy costs or comply with environmental regulations.
Which option is right for your application?
Plate Heat Exchanger
PHEs are overtaking shell and tube options in many sectors due to compactness, efficiency and ease of maintenance. If you need to efficiently heat or cool a fluid that is part of your existing process then plate heat exchangers may be the right solution for you. Learn how the construction and materials used in PHEs make them a great heat transfer source when tight on floor space.
Dimple Plate/Plate Coil
For high pressure/temperature applications that rule out the use of a traditional plate heat exchanger, a passive heat transfer application customized to fit your existing tank may be the best solution. Learn how dimple plate can be added to your tank to increase efficiency and save space at the same time.